Lo sviluppo e la tendenza della tecnologia di fusione a induzione sotto vuoto
Con il rapido sviluppo della moderna tecnologia industriale, i requisiti delle persone per l'uso di parti meccaniche stanno diventando sempre più elevati e l'ambiente di utilizzo più severo presenta requisiti più elevati per la resistenza alle alte temperature, la resistenza all'usura, la resistenza alla fatica e altre proprietà dei materiali metallici .
Per alcuni metalli specifici o materiali in lega, che si tratti di test di ricerca e sviluppo in fase iniziale o di produzione di massa in fase successiva e messa in uso, la ricerca o l'ottenimento di materiali in lega metallica ad alte prestazioni richiedono il supporto di apparecchiature per la fusione dei metalli, apparecchiature per il trattamento termico superficiale, ecc. Tra i numerosi metodi speciali di riscaldamento o fusione, la tecnologia di riscaldamento a induzione viene utilizzata per fondere e preparare materiali metallici o per sinterizzare e trattare a caldo i materiali in un determinato processo, che ha svolto un ruolo fondamentale.
Questo articolo introduce il processo di sviluppo della tecnologia di fusione a induzione sotto vuoto e l'applicazione della tecnologia di fusione a induzione in diverse occasioni. In base alla struttura dei diversi tipi di forni a induzione sotto vuoto, confrontare i loro vantaggi e svantaggi. In attesa della futura direzione di sviluppo dei forni a induzione sotto vuoto, espone il suo trend di sviluppo. Lo sviluppo e il progresso dei forni ad induzione sotto vuoto si riflettono principalmente nel graduale miglioramento della struttura complessiva delle apparecchiature, nella tendenza sempre più evidente alla modularizzazione e nel sistema di controllo più intelligente.
1. Tecnologia di fusione a induzione sotto vuoto
1.1 Principio
__kindeditor_temp_url__La tecnologia di riscaldamento a induzione di solito si riferisce a una tecnologia che utilizza il principio dell'induzione elettromagnetica per ottenere corrente di induzione per materiali con una migliore sensibilità magnetica per raggiungere lo scopo di riscaldamento in condizioni di vuoto. La corrente elettrica passa attraverso la bobina elettromagnetica che circonda il materiale metallico ad una certa frequenza. La corrente elettrica variabile genera un campo magnetico indotto, che provoca una corrente indotta nel metallo e genera una grande quantità di calore per riscaldare il materiale. Quando il calore è relativamente basso, può essere utilizzato nel trattamento termico a induzione sotto vuoto e in altri processi. Quando il calore è elevato, il calore generato è sufficiente per fondere il metallo ed essere utilizzato per preparare materiali metallici o in lega.
1.2, applicazione
1.2.1, fusione per induzione sotto vuoto
La tecnologia di fusione a induzione sotto vuoto è attualmente la tecnologia di riscaldamento a induzione più efficiente, più veloce, a basso consumo, a risparmio energetico ed ecologica per il riscaldamento di materiali metallici. Questa tecnologia è principalmente implementata nei forni fusori a induzione e in altre apparecchiature e ha una vasta gamma di applicazioni. Le materie prime metalliche solide vengono poste in un crogiolo avvolto da una bobina. Quando la corrente scorre attraverso la bobina di induzione, viene generata una forza elettromotrice indotta e viene generata una corrente parassita all'interno della carica metallica. Quando il calore attuale è maggiore della velocità di dissipazione del calore della carica metallica, il calore si accumula sempre di più Quando si raggiunge un certo livello, il metallo si fonde da uno stato solido a uno stato liquido per raggiungere lo scopo di fondere i metalli. In questo processo, poiché l'intero processo avviene in un ambiente sotto vuoto, è vantaggioso rimuovere le impurità del gas all'interno del metallo e il materiale in lega metallica ottenuto è più puro. Allo stesso tempo, durante il processo di fusione, attraverso il controllo dell'ambiente sotto vuoto e il riscaldamento a induzione, è possibile regolare la temperatura di fusione e integrare il metallo in lega in tempo per raggiungere lo scopo della raffinazione. Durante il processo di fusione, a causa delle caratteristiche della tecnologia di fusione a induzione, il materiale metallico liquido all'interno del crogiolo può essere agitato automaticamente a causa dell'interazione della forza elettromagnetica per rendere la composizione più uniforme. Questo è anche un grande vantaggio della tecnologia di fusione a induzione.
Rispetto alla fusione tradizionale, la fusione a induzione sotto vuoto presenta grandi vantaggi grazie al risparmio energetico, alla protezione dell'ambiente, al buon ambiente di lavoro per i lavoratori e alla bassa intensità di lavoro. Utilizzando la tecnologia di fusione a induzione, il materiale della lega finale è meno impuro e la proporzione della lega aggiunta è più adatta, il che può soddisfare meglio i requisiti del processo per le proprietà del materiale.
La tecnologia di fusione a induzione sotto vuoto è stata utilizzata su larga scala, dai forni a induzione di diversi chilogrammi per la ricerca sperimentale ai forni a induzione su larga scala con una capacità di decine di tonnellate per la produzione effettiva. Grazie alla sua semplice tecnologia operativa, il processo di fusione è facile da controllare e la temperatura di fusione è veloce. , Il metallo fuso ha i vantaggi di una composizione uniforme, ha grandi prospettive di applicazione ed è stato sviluppato rapidamente negli ultimi anni.
1.2.2, sinterizzazione per induzione sotto vuoto
La sinterizzazione sotto vuoto si riferisce alla sinterizzazione di polvere di metallo, lega o composto metallico in prodotti metallici e grezzi metallici a una temperatura inferiore al punto di fusione in un ambiente con un grado di vuoto di (10-10-3Pa). Sinterizzando in condizioni di vuoto, non c'è reazione tra metallo e gas e nessuna influenza del gas adsorbito. Non solo l'effetto di densificazione è buono, ma può anche svolgere un ruolo di purificazione e riduzione, riducendo la temperatura di sinterizzazione e il rapporto di sinterizzazione a temperatura ambiente può essere ridotto di 100~150 ℃, risparmiare energia, migliorare il durata del forno di sinterizzazione e ottenere prodotti di alta qualità.
Per alcuni materiali, è necessario realizzare il legame tra le particelle attraverso il trasferimento di atomi tramite riscaldamento e la tecnologia di sinterizzazione a induzione svolge un ruolo di riscaldamento in questo processo. Il vantaggio della sinterizzazione per induzione sotto vuoto è che aiuta a ridurre le sostanze nocive (vapore acqueo, ossigeno, azoto e altre impurità) nell'atmosfera in condizioni di vuoto ed evita una serie di reazioni come decarburazione, nitrurazione, cementazione, riduzione e ossidazione . Durante il processo, la quantità di gas nei pori viene ridotta e la reazione chimica delle molecole di gas viene ridotta. Allo stesso tempo, il film di ossido sulla superficie del materiale viene rimosso prima che il materiale appaia nella fase liquida, in modo che il materiale sia più densamente legato quando il materiale viene fuso e incollato e la sua resistenza all'usura sia migliorata. forza. Inoltre, la sinterizzazione per induzione sotto vuoto ha anche un certo effetto sulla riduzione dei costi del prodotto.
Poiché il contenuto di gas è relativamente basso in un ambiente sotto vuoto, la convezione e la conduzione del calore possono essere ignorate. Il calore viene trasferito principalmente dal componente riscaldante alla superficie del materiale sotto forma di radiazione. La selezione si basa sulla temperatura di sinterizzazione specifica e sulle proprietà fisiche e chimiche del materiale. Anche i componenti di riscaldamento appropriati sono molto importanti. Rispetto al riscaldamento a resistenza al vuoto, la sinterizzazione a induzione adotta il riscaldamento a potenza a frequenza intermedia, che evita il problema dell'isolamento ad alta temperatura dei forni a vuoto che utilizzano il riscaldamento a resistenza in una certa misura.
Attualmente, la tecnologia di sinterizzazione a induzione è utilizzata principalmente nei settori dell'acciaio e della metallurgia. Inoltre, su speciali materiali ceramici, la sinterizzazione a induzione migliora il legame delle particelle solide, aiuta la crescita dei grani di cristallo, comprime i vuoti e quindi aumenta la densità per formare corpi sinterizzati policristallini densi. La tecnologia della sinterizzazione a induzione è anche più ampiamente utilizzata nella ricerca di nuovi materiali.
1.2.3, trattamento termico a induzione sotto vuoto
Al momento, dovrebbe esserci più tecnologia di trattamento termico a induzione principalmente concentrata nella tecnologia di tempra a induzione. Metti il pezzo nell'induttore (bobina), quando una corrente alternata di una certa frequenza passa attraverso l'induttore, attorno ad esso verrà generato un campo magnetico alternato. L'induzione elettromagnetica del campo magnetico alternato produce una corrente parassita chiusa nel pezzo. A causa dell'effetto pelle, cioè la distribuzione della corrente indotta sulla sezione trasversale del pezzo è molto irregolare, la densità di corrente sulla superficie del pezzo è molto alta e diminuisce gradualmente verso l'interno.
L'energia elettrica della corrente ad alta densità sulla superficie del pezzo viene convertita in energia termica, che aumenta la temperatura della superficie, cioè realizza il riscaldamento della superficie. Maggiore è la frequenza di corrente, maggiore è la differenza di densità di corrente tra la superficie e l'interno del pezzo e più sottile è lo strato riscaldante. Dopo che la temperatura dello strato riscaldante supera la temperatura del punto critico dell'acciaio, viene rapidamente raffreddato per ottenere la tempra superficiale. Dal principio del riscaldamento a induzione si può sapere che la profondità di penetrazione della corrente può essere opportunamente modificata regolando la frequenza della corrente attraverso la bobina di induzione. La profondità regolabile è anche un grande vantaggio del trattamento termico a induzione. Tuttavia, la tecnologia di tempra a induzione non è adatta per pezzi meccanici complicati a causa della sua scarsa adattabilità. Sebbene lo strato superficiale del pezzo temprato abbia una maggiore sollecitazione interna di compressione, la resistenza alla frattura per fatica è maggiore. Ma è adatto solo per la produzione in catena di montaggio di pezzi semplici.
Attualmente, l'applicazione della tecnologia di tempra a induzione viene utilizzata principalmente nella tempra superficiale della manovellaalberos e camalberos nel settore automobilistico. Sebbene queste parti abbiano una struttura semplice, ma l'ambiente di lavoro è duro, hanno un certo grado di resistenza all'usura, resistenza alla flessione e resistenza alle prestazioni delle parti. I requisiti di fatica, attraverso la tempra a induzione per migliorare la loro resistenza all'usura e la resistenza alla fatica è anche il metodo più ragionevole per soddisfare i requisiti di prestazione. È ampiamente usato in trattamento della superficie di alcune parti dell'industria automobilistica.
2. Apparecchiatura di fusione a induzione sotto vuoto
L'attrezzatura di fusione a induzione sotto vuoto utilizza la tecnologia di fusione a induzione per realizzare il principio nell'uso effettivo attraverso l'abbinamento della struttura meccanica. L'apparecchiatura di solito utilizza il principio dell'induzione elettromagnetica per mettere la bobina di induzione e il materiale in una cavità chiusa ed estrarre il gas nel contenitore attraverso un sistema di pompaggio del vuoto, quindi utilizzare l'alimentazione per far passare la corrente attraverso la bobina di induzione per generare una forza elettromotrice indotta ed essere all'interno del materiale Si forma un vortice e quando la generazione di calore raggiunge un certo livello, il materiale inizia a fondere. Durante il processo di fusione, una serie di operazioni come il controllo della potenza, la misurazione della temperatura, la misurazione del vuoto e l'alimentazione supplementare vengono realizzate attraverso altri componenti di supporto sull'attrezzatura, e infine il metallo liquido viene versato nello stampo attraverso l'inversione del crogiolo per formare un lingotto di metallo. odore. La struttura principale dell'attrezzatura per la fusione a induzione sotto vuoto comprende le seguenti parti:
Oltre ai componenti di cui sopra, il forno di fusione sotto vuoto dovrebbe anche essere dotato di un alimentatore, un sistema di controllo e un sistema di raffreddamento per fornire energia all'attrezzatura per fondere il materiale e fornire una certa quantità di raffreddamento nelle parti chiave per evitare che il sistema si surriscaldi con conseguente riduzione della vita strutturale o danni. Per le apparecchiature di fusione a induzione con requisiti di processo specifici, ci sono componenti ausiliari correlati, come carrello di trasmissione, apertura e chiusura della porta del forno, piatto di colata centrifuga, finestra di osservazione, ecc. Per le apparecchiature con più impurità, dovrebbe anche essere dotato di un filtro del gas sistema, ecc. Si può vedere che, oltre ai componenti necessari, un set completo di apparecchiature per la fusione a induzione può anche realizzare diverse funzioni aggiungendo altri componenti in base a requisiti di processo specifici e fornire condizioni convenienti e metodi di implementazione per la preparazione del metallo.
2.1. Forno fusorio a induzione sotto vuoto
Il forno di fusione a induzione sotto vuoto è un'apparecchiatura di fusione che prima fonde il metallo mediante riscaldamento a induzione sotto vuoto, quindi versa il metallo liquido in uno stampo per ottenere un lingotto di metallo. Lo sviluppo dei forni ad induzione sotto vuoto iniziò intorno al 1920 ed era principalmente utilizzato per fondere le leghe di nichel-cromo. Fino a quando la seconda guerra mondiale non ha promosso il progresso della tecnologia del vuoto, il forno di fusione a induzione sotto vuoto è stato veramente sviluppato. Durante questo periodo, a causa della domanda di materiali in lega, i forni fusori a induzione sotto vuoto hanno continuato a svilupparsi su larga scala, dalle iniziali diverse tonnellate a dozzine di tonnellate di forni a induzione ultra-grandi. Per adattarsi alla produzione di massa, oltre al cambiamento della capacità delle attrezzature, anche la struttura del forno a induzione si è evoluta da un forno a ciclo con un ciclo come unità a una fusione a induzione sotto vuoto continua o semicontinua per il caricamento, lo stampo operazioni di preparazione, fusione e colata. Il funzionamento continuo senza fermare il forno consente di risparmiare il tempo di carica e il tempo di attesa per il raffreddamento del lingotto. La produzione continua aumenta l'efficienza e aumenta anche la produzione di lega. Soddisfare meglio le esigenze della produzione effettiva. Rispetto ai paesi stranieri, i primi forni a induzione sotto vuoto nel mio paese hanno una capacità relativamente piccola, principalmente sotto le 2 tonnellate. I grandi forni fusori fanno ancora affidamento sulle importazioni dall'estero. Con lo sviluppo degli ultimi decenni, il mio paese può anche sviluppare da solo la fusione a induzione sotto vuoto su larga scala. Forno, la fusione massima raggiunge più di dieci tonnellate. Il forno fusorio a induzione sotto vuoto VIM sviluppato in precedenza, con struttura semplice, uso conveniente e bassi costi di manutenzione ed è stato ampiamente utilizzato nella produzione effettiva.
La forma base di un forno fusorio a induzione sotto vuoto. I materiali metallici vengono aggiunti al crogiolo di fusione tramite una torretta girevole. L'altro lato è allineato con il crogiolo e la misurazione della temperatura viene effettuata inserendo la termocoppia nel metallo fuso. Il metallo fuso viene azionato dal meccanismo di rotazione e versato nello stampo di formatura per realizzare la fusione del metallo. L'intero processo è semplice e comodo da usare. Ogni fusione richiede uno o due lavoratori per essere completata. Durante il processo di fusione, è possibile ottenere il monitoraggio della temperatura in tempo reale e la regolazione della composizione del materiale e il materiale metallico finale è più in linea con i requisiti del processo.
2.2. Forno a gas a membrana a induzione sotto vuoto
Per alcuni materiali, non è necessario completare il versamento in una camera a vuoto nel processo, sono richiesti solo la conservazione del calore e il degasaggio in un ambiente sotto vuoto. Sulla base del forno VIM, viene gradualmente sviluppato il forno a gas a membrana a induzione sotto vuoto del forno di degasaggio VID.
La caratteristica principale del forno di degasaggio a induzione sotto vuoto è la struttura compatta e il piccolo volume del forno. Un volume più piccolo favorisce una rapida estrazione del gas e un vuoto migliore. Rispetto ai forni di degasaggio convenzionali, l'apparecchiatura ha un volume relativamente piccolo, una bassa perdita di temperatura, una migliore flessibilità ed economia ed è adatta per l'alimentazione di liquidi o solidi. Il forno VID può essere utilizzato per la fusione e il degasaggio di acciai speciali e metalli non ferrosi e necessita di essere colato nello stampo in condizioni di ambiente atmosferico o atmosfera protettiva. L'intero processo di fusione può realizzare la rimozione di impurità come la decarburazione e la raffinazione dei materiali, la deidrogenazione, la disossidazione e la desolforazione, che è favorevole alla regolazione precisa della composizione chimica per soddisfare i requisiti del processo.
In una certa condizione di vuoto o atmosfera protettiva, il materiale metallico viene gradualmente fuso dal riscaldamento del forno di degasaggio a induzione e il gas interno può essere rimosso in questo processo. Se nel processo viene aggiunto un gas di reazione appropriato, si unirà all'elemento carbonio all'interno del metallo per generare carburi gassosi da rimuovere dal forno, raggiungendo lo scopo di decarburazione e raffinazione. Nel processo di colata, è necessario introdurre una certa atmosfera protettiva per garantire che il materiale metallico che è stato degasato sia isolato dal gas nell'atmosfera e, infine, il degasaggio e la raffinazione del materiale metallico siano completati.
2.3. Forno di colata di degasaggio a induzione sotto vuoto
Il forno di colata di degasaggio ad induzione sotto vuoto è sviluppato sulla base delle prime due tecnologie di fusione. Nel 1988, Leybold-Heraeus, il predecessore dell'azienda tedesca ALD, ha prodotto il primo forno VIDP. Il cuore tecnico di questo tipo di forno è una camera di fusione sottovuoto compatta integrata con il crogiolo della bobina di induzione. È solo un po' più grande della bobina di induzione e contiene solo la bobina di induzione e il crogiolo. Cavi, tubazioni di raffreddamento ad acqua e meccanismo di ribaltamento idraulico sono tutti installati all'esterno della camera di fusione. Il vantaggio è quello di proteggere i cavi e le tubazioni raffreddate ad acqua dai danni causati da schizzi di acciaio fuso e da variazioni periodiche di temperatura e pressione. A causa della comodità dello smontaggio e della facilitazione della sostituzione del crogiolo, l'involucro del forno VIDP è dotato di tre corpi del forno. Un rivestimento del forno a crogiolo di preparazione accorcia il ciclo di produzione e migliora l'efficienza produttiva.
La copertura del forno è supportata sul telaio del forno e su due colonne del cilindro idraulico mediante sigillatura sottovuoto cuscinettoS. Durante il versamento, due cilindri idraulici sormontano lateralmente il coperchio del forno e il coperchio del forno aziona la camera di fusione per inclinarsi attorno al vuoto cuscinetto. Nello stato di colata inclinata, non c'è movimento relativo tra la camera di fusione e il crogiolo della bobina di induzione. Il canale è una parte importante del forno VIDP. Poiché il design del forno VIDP isola la camera di fusione dalla camera del lingotto, l'acciaio fuso deve passare attraverso il canale del vuoto nella camera del lingotto. La camera del lingotto è aperta e chiusa con un lato obliquo quadrato. È composto da due parti. La parte fissa è adiacente alla camera di scorrimento e la parte mobile si sposta orizzontalmente lungo il binario a terra per completare l'apertura e la chiusura della camera di lingottiera. In alcune apparecchiature, la parte mobile è progettata per essere di 30 gradi, aperta a sinistra ea destra verso l'alto, il che è conveniente per il carico e lo scarico delle lingottiere e la manutenzione e riparazione quotidiana delle gru. All'inizio della fusione, il corpo del forno viene sollevato dal meccanismo idraulico sottostante, unito alla struttura superiore del coperchio del forno e bloccato con un meccanismo speciale. L'estremità superiore del coperchio del forno è collegata alla camera di alimentazione tramite un vuoto valvola.
Poiché solo la parte di fusione è racchiusa nella camera del vuoto e versata attraverso la scanalatura di deviazione, la struttura del forno è compatta, la camera di fusione è più piccola e il vuoto può essere controllato meglio e più velocemente. Rispetto al tradizionale forno fusorio ad induzione, ha le caratteristiche di breve tempo di evacuazione e bassa percentuale di perdite. Il controllo della pressione ideale può essere ottenuto dotando il sistema di controllo logico PLC. Allo stesso tempo, il sistema di agitazione elettromagnetica può agitare stabilmente il bagno fuso e gli elementi aggiunti verranno dissolti uniformemente nel bagno fuso dall'alto verso il basso, mantenendo la temperatura vicino alla costante. Quando si versa il denaro, il canale viene riscaldato dal sistema di riscaldamento esterno per ridurre il blocco di versamento iniziale dell'apertura di versamento e il cracking termico del canale. Aggiungendo il deflettore del filtro e altre misure, può alleviare l'impatto dell'acciaio fuso e migliorare la purezza del metallo. A causa del piccolo volume del forno VIDP, il rilevamento e la riparazione delle perdite di vuoto sono più facili e il tempo di pulizia nel forno è più breve. Inoltre, la temperatura nel forno può essere misurata con una piccola termocoppia facile da sostituire.
2.4, crogiolo raffreddato ad acqua a induzione
Il metodo di fusione a levitazione sotto vuoto a induzione elettromagnetica del crogiolo raffreddato ad acqua è un metodo di fusione che si è sviluppato rapidamente negli ultimi anni. Viene principalmente utilizzato per preparare materiali metallici o non metallici ad alto punto di fusione, elevata purezza ed estremamente attivi. Tagliando il crogiolo di rame in parti uguali della struttura del petalo di rame, e il raffreddamento ad acqua passa attraverso ogni blocco di petali, questa struttura migliora la spinta elettromagnetica, in modo che il metallo fuso venga schiacciato nel mezzo per formare una gobba e staccarsi dal parete del crogiolo. Il metallo è posto in un campo elettromagnetico alternato. Il dispositivo concentra la capacità nello spazio del volume all'interno del crogiolo e quindi forma una forte corrente parassita sulla superficie della carica. Da un lato, rilascia calore Joule per sciogliere la carica, e dall'altro forma la forza di Lorentz per fondere. Il corpo sospende e produce una forte agitazione. Gli elementi di lega aggiunti possono essere miscelati rapidamente e in modo uniforme nel fuso, rendendo la composizione chimica più uniforme e la conduzione della temperatura più equilibrata. A causa dell'effetto della levitazione magnetica, il fuso non è in contatto con la parete interna del crogiolo, il che impedisce al crogiolo di inquinare il fuso. Allo stesso tempo, riduce la conduzione del calore e migliora la radiazione termica, che riduce la dissipazione del calore del metallo fuso e raggiunge una temperatura più elevata. Per la carica metallica aggiunta, può essere fusa e tenuta in caldo secondo il tempo richiesto e la temperatura impostata, e la carica non necessita di essere elaborata in anticipo. La fusione a crogiolo raffreddata ad acqua può raggiungere il livello della fusione a fascio di elettroni in termini di rimozione di inclusioni metalliche e raffinazione di degasaggio, mentre la perdita per evaporazione è inferiore, il consumo di energia è inferiore e l'efficienza di produzione è migliorata. A causa delle caratteristiche di riscaldamento senza contatto del riscaldamento a induzione, l'impatto sul fuso è minore e ha un buon effetto sulla preparazione di metalli di maggiore purezza o estremamente attivi. A causa della complessa struttura dell'apparecchiatura, è ancora difficile realizzare la fusione a maglev per apparecchiature di grande capacità. In questa fase, non sono disponibili apparecchiature di fusione a crogiolo di rame raffreddate ad acqua di grande capacità. L'attuale attrezzatura a crogiolo raffreddato ad acqua viene utilizzata solo per la ricerca sperimentale sulla fusione di metalli in piccoli volumi.
3. Il futuro trend di sviluppo delle apparecchiature per la fusione a induzione
Con lo sviluppo della tecnologia di riscaldamento a induzione sotto vuoto, i tipi di forni cambiano costantemente per ottenere funzioni diverse. Da semplice struttura di fusione o riscaldamento, si è gradualmente evoluta in una struttura complessa che può svolgere diverse funzioni ed è più favorevole alla produzione. Per processi tecnologici più complessi in futuro, come ottenere un controllo preciso del processo, misurare ed estrarre informazioni rilevanti e ridurre il più possibile i costi di manodopera è la direzione di sviluppo delle apparecchiature di fusione a induzione.
3.1, modulare
In un set completo di apparecchiature, diversi componenti sono attrezzati per diverse esigenze di utilizzo. Ogni parte del componente svolge la propria funzione per raggiungere il proprio scopo d'uso. Per alcuni tipi di forno, l'aggiunta di determinati moduli per rendere l'attrezzatura più completa, ad esempio dotata di un sistema completo di misurazione della temperatura, aiuta a osservare i cambiamenti dei materiali nel forno con la temperatura e ad ottenere un controllo più ragionevole della temperatura; dotato di uno spettrometro di massa per rilevare la composizione del materiale Regolare il tempo e la sequenza di aggiunta di elementi di lega per migliorare le prestazioni della lega nella fase di sviluppo del processo; dotato di cannone elettronico e cannone ionico per risolvere il problema della fusione di alcuni metalli refrattari, e così via. Nelle future apparecchiature metallurgiche a induzione, diverse combinazioni di moduli diversi per ottenere funzioni diverse e soddisfare requisiti di processo diversi sono diventate un'inevitabile tendenza di sviluppo, ed è anche una combinazione e un riferimento di diversi campi. Al fine di migliorare il processo di fusione dei metalli e ottenere materiali con prestazioni migliori, le apparecchiature modulari avranno una maggiore competitività sul mercato.
3.2. Controllo intelligente
Rispetto alla fusione tradizionale, l'attrezzatura per l'induzione sotto vuoto presenta un grande vantaggio nella realizzazione del controllo del processo. Grazie allo sviluppo della tecnologia informatica, il funzionamento intuitivo dell'interfaccia uomo-macchina, l'acquisizione intelligente del segnale e l'impostazione ragionevole del programma nell'apparecchiatura possono facilmente raggiungere lo scopo di controllare il processo di fusione, ridurre i costi di manodopera e rendere l'operazione più semplice e conveniente.
Nello sviluppo futuro, alle apparecchiature per il vuoto verranno aggiunti sistemi di controllo più intelligenti. Per il processo stabilito, sarà più facile per le persone controllare con precisione la temperatura di fusione attraverso il sistema di controllo intelligente, aggiungere materiali in lega in un momento specifico e completare una serie di azioni di fusione, conservazione del calore e colata. E tutto questo sarà controllato e registrato dal computer, riducendo inutili perdite causate da errori umani. Per il processo di fusione ripetitivo, può realizzare un controllo moderno più conveniente e intelligente.
3.3. Informatizzazione
Le apparecchiature di fusione a induzione genereranno una grande quantità di informazioni di fusione durante l'intero processo di fusione, le modifiche dei parametri in tempo reale dell'alimentatore di riscaldamento a induzione, il campo di temperatura della carica, il crogiolo, il campo elettromagnetico generato dalla bobina di induzione, il proprietà fisiche del metallo fuso e così via. Al momento, l'apparecchiatura realizza solo una semplice raccolta di dati e il processo di analisi viene eseguito dopo che i dati sono stati estratti al termine della fusione. In futuro, lo sviluppo dell'informatizzazione, la raccolta e l'elaborazione dei dati e il processo di analisi saranno inevitabilmente quasi sincronizzati con il processo di fusione. Raccolta completa dei dati per i materiali fusi internamente delle apparecchiature metallurgiche, elaborazione dei dati al computer, visualizzazione in tempo reale del campo di temperatura interno e del campo elettromagnetico dell'apparecchiatura nella situazione attuale e trasmissione del segnale, tramite feedback in tempo reale di diversi dati, conveniente per le persone L'osservazione e la regolazione in tempo reale del processo di fusione hanno rafforzato l'intervento umano e il controllo. Nel processo di fusione, vengono apportate modifiche tempestive per migliorare il processo e migliorare le prestazioni della lega.
Conclusione 4
Con il progresso dell'industria, la tecnologia di fusione a induzione sotto vuoto si è sviluppata enormemente negli ultimi decenni con i suoi vantaggi unici e svolge un ruolo importante nel campo industriale. Al momento, sebbene la tecnologia di fusione a induzione sotto vuoto del mio paese sia ancora in ritardo rispetto ai paesi stranieri, richiede ancora gli sforzi incessanti dei professionisti competenti per migliorare la competitività sul mercato delle attrezzature di fusione speciali del mio paese e fare del suo meglio per diventare l'attrezzatura di fusione di prima classe al mondo . All'avanguardia.
Link a questo articolo: Lo sviluppo e la tendenza della tecnologia di fusione a induzione sotto vuoto
Dichiarazione di ristampa: se non ci sono istruzioni speciali, tutti gli articoli su questo sito sono originali. Si prega di indicare la fonte per la ristampa: https://www.cncmachiningptj.com
PTJ® è un produttore personalizzato che fornisce una gamma completa di barre di rame, parti in ottone ed parti in rame. I processi di produzione comuni includono tranciatura, goffratura, lavorazione del rame, servizi di filo edm, incisione, formatura e piegatura, ricalcatura, caldo forgiatura e pressatura, perforazione e punzonatura, rullatura e godronatura, tranciatura, lavorazione multimandrino, estrusione e forgiatura del metallo ed stampigliatura. Le applicazioni includono sbarre collettrici, conduttori elettrici, cavi coassiali, guide d'onda, componenti di transistor, tubi a microonde, tubi per stampi vuoti e metallurgia delle polveri vasche di estrusione.
Raccontaci un po' del budget del tuo progetto e dei tempi di consegna previsti. Faremo una strategia con te per fornire i servizi più convenienti per aiutarti a raggiungere il tuo obiettivo, non esitare a contattarci direttamente ( vendite@pintejin.com ).
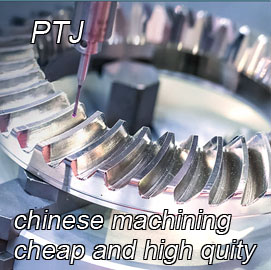
- Lavorazione a 5 assi
- Fresatura a controllo numerico
- Tornitura cnc
- Industrie di lavorazione
- Processo di lavorazione
- Trattamento della superficie
- Lavorazione dei metalli
- Lavorazione plastica
- Stampo per metallurgia delle polveri
- Die Casting
- Galleria delle parti
- Parti metalliche per auto
- Pezzi meccanici
- Dissipatore di calore a LED
- Parti di costruzione
- Parti mobili
- Parti mediche
- Parti elettroniche
- Lavorazione su misura
- Parti di biciclette
- Lavorazione dell'alluminio
- Lavorazione del titanio
- Lavorazione dell'acciaio inossidabile
- Lavorazione del rame
- Lavorazione dell'ottone
- Lavorazione Super Lega
- Peek lavorazione
- Lavorazione UHMW
- Lavorazione Unilate
- Lavorazione PA6
- Lavorazione PPS
- Lavorazione Teflon
- Lavorazione Inconel
- Lavorazione dell'acciaio per utensili
- Più materiale