Come assemblare e installare macchine utensili CNC nel modo giusto e buoni consigli
2023-10-30
Capitolo 1: Comprendere le macchine CNC
In questo capitolo getteremo le basi esplorando cosa sono le macchine CNC, i vari tipi disponibili e i componenti chiave che compongono una macchina CNC.UN. Cos'è una macchina CNC?
Una macchina CNC, abbreviazione di macchina a controllo numerico computerizzato, è un'apparecchiatura sofisticata utilizzata nella produzione e processo di lavorazionees. A differenza delle macchine convenzionali azionate manualmente da operatori umani, le macchine CNC sono automatizzate e controllate da computer, consentendo operazioni precise e altamente ripetibili. Queste macchine sono in grado di eseguire attività complesse come taglio, foratura, fresatura e modellatura di materiali come metallo, plastica, legno e altro ancora. Al centro di una macchina CNC c'è la sua capacità di interpretare ed eseguire comandi provenienti da software di progettazione assistita da computer (CAD) o di produzione assistita da computer (CAM). Questo software genera una serie di codici numerici, spesso indicati come codici G e codici M, che istruiscono la macchina CNC su come spostare gli utensili da taglio e il pezzo in lavorazione per ottenere il risultato desiderato. Le macchine CNC hanno rivoluzionato le industrie manifatturiere aumentando l’efficienza, riducendo l’errore umano e consentendo la produzione di componenti complessi e personalizzati.B. Tipi di macchine CNC
Le macchine CNC sono disponibili in vari tipi, ciascuno progettato per applicazioni e settori specifici. Ecco alcuni tipi comuni di macchine CNC:- Fresatura CNC macchine: Queste macchine vengono utilizzate per tagliare e modellare i materiali mediante utensili da taglio rotanti. Sono ampiamente utilizzati in settori quali quello aerospaziale, automobilistico e della lavorazione dei metalli per attività quali foratura, fresatura e incisione.
- Torni CNC: I torni CNC sono progettati per ruotare il pezzo mentre un utensile da taglio viene utilizzato per rimuovere il materiale da esso. Sono essenziali per la produzione di componenti cilindrici, come ad es alberos e boccolas.
- Router CNC: Queste macchine vengono utilizzate principalmente per tagliare e modellare materiali come legno, plastica e compositi. I router CNC sono comuni nelle industrie della lavorazione del legno e della segnaletica.
- Taglierine al plasma CNC: Ideali per il taglio di lamiere, le macchine da taglio al plasma CNC utilizzano un getto di gas ionizzato ad alta velocità per sciogliere e rimuovere il materiale. Sono impiegati nella lavorazione dei metalli e nell'industria automobilistica.
- Taglierine laser CNC: Le macchine da taglio laser utilizzano un raggio laser ad alta potenza per tagliare o incidere con precisione vari materiali, inclusi metalli, plastica e tessuti. Trovano applicazioni in settori che vanno dalla gioielleria alla produzione industriale.
- Taglierine a getto d'acqua CNC: Le taglierine a getto d'acqua utilizzano un flusso d'acqua ad alta pressione mescolato con particelle abrasive per tagliare i materiali. Sono adatti per tagliare un'ampia gamma di materiali, tra cui pietra, vetro e metalli.
- Macchine per elettroerosione CNC: Le macchine per elettroerosione (EDM) utilizzano scariche elettriche per erodere il materiale dal pezzo. Sono utilizzati per compiti complessi e di alta precisione, soprattutto nella costruzione di utensili e matrici.
C. Componenti di una macchina CNC
Comprendere i componenti di una macchina CNC è fondamentale per un funzionamento e una manutenzione efficaci. Ecco i componenti chiave presenti nella maggior parte delle macchine CNC:- Telaio della macchina: Il telaio della macchina fornisce il supporto strutturale per l'intera macchina CNC. In genere è realizzato con materiali resistenti per garantire stabilità e rigidità durante il funzionamento.
- Mandrino: Il mandrino è un componente motorizzato responsabile del sostegno e della rotazione degli utensili da taglio o degli accessori. Svolge un ruolo fondamentale nella precisione e nella velocità del processo di lavorazione.
- Sistema di assi: Le macchine CNC operano lungo più assi, solitamente etichettati come X, Y e Z. Questi assi definiscono il movimento della macchina nello spazio tridimensionale. Alcune macchine possono avere assi di rotazione aggiuntivi, come A, B e C, per operazioni più complesse.
- Cambio utensile: Molte macchine CNC sono dotate di cambio utensile automatico che consente il rapido cambio degli utensili da taglio durante un processo di lavorazione. Ciò migliora l’efficienza e riduce i tempi di inattività.
- Pannello di controllo: Il pannello di controllo contiene l'interfaccia attraverso la quale gli operatori o i programmatori possono inserire comandi, caricare programmi e monitorare lo stato della macchina.
- Piano di lavoro o sistema di sostegno: Il piano di lavoro è il luogo in cui il pezzo viene tenuto saldamente in posizione durante la lavorazione. Vari dispositivi di bloccaggio del pezzo, come morsetti, morse e infissi, vengono utilizzati per garantire che il pezzo rimanga stabile e posizionato correttamente.
- Sistema di guida: Il sistema di azionamento comprende motori e attuatori responsabili del movimento dei componenti della macchina lungo gli assi specificati. Il controllo preciso del sistema di azionamento è essenziale per una lavorazione accurata.
- Sistema refrigerante: Il raffreddamento è vitale durante Lavorazione CNC multiasse per evitare il surriscaldamento degli utensili e dei pezzi in lavorazione. Le macchine CNC spesso dispongono di un sistema di raffreddamento per mantenere la temperatura ottimale.
- Computer di controllo: Il computer di controllo ospita l'hardware e il software necessari per il funzionamento della macchina CNC. Interpreta i codici G e M generati dal software CAD/CAM e li converte in movimenti e azioni.
Capitolo 2: Preparazione pre-installazione
Prima di intraprendere l'installazione della tua macchina CNC, è fondamentale effettuare preparativi approfonditi. Questo capitolo guiderà l'utente attraverso le considerazioni essenziali prima dell'installazione, tra cui la configurazione dell'area di lavoro, i requisiti elettrici e di alimentazione e le misure di sicurezza per garantire un processo di installazione agevole e sicuro.UN. Considerazioni sull'area di lavoro
- Requisiti di spazio: Inizia valutando lo spazio disponibile nella tua officina o struttura. Assicurarsi che l'area sia sufficientemente spaziosa per ospitare la macchina CNC, compreso spazio sufficiente per l'accesso e la manutenzione sicuri. Considerare le dimensioni della macchina, lo spazio richiesto per la movimentazione dei materiali e qualsiasi attrezzatura o postazione di lavoro aggiuntiva.
- Ventilazione: Una ventilazione adeguata è fondamentale per dissipare il calore generato durante la lavorazione e per rimuovere eventuali fumi o particelle di polvere potenzialmente dannose. Installare adeguati sistemi di ventilazione o apparecchiature di filtraggio dell'aria secondo necessità per mantenere un ambiente di lavoro pulito e sicuro.
- Pavimentazione: Assicurarsi che il pavimento nell'area designata sia livellato, stabile e in grado di sostenere il peso della macchina CNC. Una pavimentazione irregolare o debole può provocare vibrazioni e imprecisioni della macchina durante il funzionamento.
- Accessibilità: Pianificare un facile accesso alla macchina CNC per installazione, manutenzione e riparazione. Assicurarsi che vi siano percorsi liberi e spazio sufficiente per manovrare macchinari e materiali pesanti.
- Illuminazione: Un’illuminazione adeguata è essenziale per un funzionamento sicuro e accurato. Assicurarsi che l'area di lavoro sia ben illuminata per prevenire incidenti e fornire una chiara visibilità del processo di lavorazione.
B. Requisiti elettrici e di alimentazione
- Fornitura elettrica: Determina i requisiti elettrici specifici della tua macchina CNC. Controlla le specifiche tecniche della macchina e consulta il produttore o il fornitore per garantire che l'alimentazione elettrica della tua struttura soddisfi questi requisiti.
- Voltaggio e Fase: Le macchine CNC possono richiedere diversi livelli di tensione (ad esempio, 110 V, 220 V, 440 V) e fasi (monofase o trifase). Assicurarsi che l'alimentazione elettrica corrisponda alle specifiche della macchina.
- Pannello elettrico: Installare un quadro elettrico dedicato per la macchina CNC per evitare di sovraccaricare i circuiti esistenti. Assumere un elettricista autorizzato per gestire il cablaggio e i collegamenti in modo professionale.
- Protezione contro le sovratensioni: Investi in dispositivi di protezione contro le sovratensioni per salvaguardare i componenti elettronici sensibili della macchina CNC da fluttuazioni di tensione e sovratensioni elettriche.
- Messa a terra: Garantire un'adeguata messa a terra sia della macchina CNC che dell'impianto elettrico per mitigare il rischio di rischi elettrici e danni alle apparecchiature.
C. Misure di sicurezza
- Equipaggiamento di sicurezza: Dare priorità alla sicurezza fornendo adeguati dispositivi di protezione individuale (DPI) per operatori e tecnici. Ciò può includere occhiali di sicurezza, protezioni per l'udito, guanti e indumenti protettivi.
- Procedure di emergenza: Sviluppare e documentare procedure di arresto di emergenza che possano arrestare rapidamente la macchina CNC in caso di eventi o incidenti imprevisti. Assicurarsi che tutto il personale sia addestrato su queste procedure.
- Sicurezza antincendio: Installare estintori e rilevatori di fumo in prossimità della macchina CNC. Implementare protocolli di sicurezza antincendio, come tenere i materiali infiammabili lontano dalla macchina e mantenere un piano di uscita antincendio.
- Blocco/Tagout (LOTO): Implementare le procedure LOTO per prevenire l'avvio accidentale della macchina durante la manutenzione o la riparazione. Utilizza lucchetti e tag per indicare quando una macchina è in fase di manutenzione.
- Allenamento di sicurezza: Condurre una formazione completa sulla sicurezza per tutto il personale che utilizzerà, manterrà o lavorerà attorno alla macchina CNC. Enfatizzare le pratiche sicure e l’importanza di seguire i protocolli di sicurezza.
- Primo soccorso: Tenere un kit di pronto soccorso ben fornito nelle vicinanze della macchina CNC. Assicurarsi che sia disponibile personale addestrato per fornire il primo soccorso immediato in caso di infortuni.
Capitolo 3: Assemblaggio della macchina CNC
Una volta completati i preparativi pre-installazione, è il momento di passare alla fase di montaggio. In questo capitolo forniremo una guida passo passo sull'assemblaggio della macchina CNC, coprendo le attività essenziali dal disimballaggio e ispezione alla gestione dei cavi.UN. Disimballaggio e ispezione
- unboxing: Inizia disimballando attentamente tutti i componenti della tua macchina CNC. Seguire le istruzioni del produttore per il disimballaggio per evitare danni durante il processo. Se necessario, utilizzare strumenti e attrezzature di sollevamento adeguati.
- Inventario dei componenti: Crea una lista di controllo dell'inventario per assicurarti di aver ricevuto tutti i componenti elencati nel manuale o nella documentazione della macchina. Verificare che nulla manchi o sia danneggiato.
- Ispezionare per danni: Esaminare attentamente ciascun componente per eventuali segni di danno, come ammaccature, graffi o parti piegate. Documentare eventuali problemi e informare immediatamente il produttore o il fornitore.
B. Organizzazione dei componenti
- Organizza l'area di lavoro: Prima del montaggio, assicurati che il tuo spazio di lavoro sia pulito e ben organizzato. Elimina ogni disordine e fornisci ampio spazio per disporre e organizzare i componenti.
- Raggruppa parti simili: Raggruppare insieme parti simili per facilitare il processo di assemblaggio. Componenti come fissaggioSupporti, staffe e hardware devono essere organizzati in contenitori o vassoi separati per un facile accesso.
- Fare riferimento ai manuali: Esaminare i manuali di assemblaggio e la documentazione fornita dal produttore. Acquisire familiarità con le fasi di assemblaggio, i diagrammi e le eventuali istruzioni specifiche.
C. Assemblaggio del telaio della macchina
- Assemblea di base: Inizia con la base della macchina CNC. Seguire le istruzioni del produttore per montare saldamente il telaio di base. Assicurarsi che sia livellato e stabile.
- Colonne e strutture di supporto: Assemblare le colonne e le strutture di sostegno, allineandole accuratamente alla base. Stringere tutti i bulloni e gli elementi di fissaggio ai valori di coppia consigliati.
- Guide e rotaie: Installare le guide e i binari che guideranno il movimento dei componenti di taglio o di supporto degli utensili della macchina. Assicurarsi che siano correttamente allineati e fissati saldamente.
D. Collegamento di motori e azionamenti
- Installazione del motore: Montare i motori nelle posizioni designate secondo le istruzioni del produttore. Assicurarsi che i motori siano fissati saldamente e allineati con i meccanismi di azionamento.
- Sistema di guida: Collegare i motori ai meccanismi di azionamento mediante appositi giunti o cinghie. Garantire la tensione e l'allineamento corretti per evitare giochi e imprecisioni.
e. Installazione del pannello di controllo
- Montaggio del pannello di controllo: Installare il pannello di controllo in una posizione comoda, solitamente facilmente raggiungibile dall'operatore. Assicurarsi che sia montato e posizionato saldamente per una visibilità e un'accessibilità ottimali.
- Connessione elettrica: Collegare il pannello di controllo all'impianto elettrico della macchina seguendo gli schemi elettrici forniti nella documentazione del produttore. Ricontrollare la precisione di tutte le connessioni.
F. Gestione dei cavi
- Instradamento dei cavi: Disporre con attenzione tutti i cavi, i fili e i tubi flessibili in modo organizzato per evitare grovigli o interferenze con le parti in movimento. Utilizzare passerelle o clip per fissare e proteggere i cavi.
- etichettatura: Etichetta cavi e fili con contrassegni o etichette identificativi per semplificare la risoluzione dei problemi e la manutenzione. Contrassegnare chiaramente lo scopo e la destinazione di ciascun cavo.
- Test: Prima di chiudere eventuali involucri o pannelli, eseguire un test preliminare per garantire che tutti i collegamenti elettrici funzionino correttamente. Verificare che motori e sensori rispondano come previsto.
Capitolo 4: Allineamento e livellamento
Nel capitolo 4 approfondiremo il processo critico di allineamento e livellamento della macchina CNC. Il corretto allineamento e livellamento sono fondamentali per garantire l'accuratezza e la precisione delle operazioni della macchina. Questo capitolo tratta l'importanza dell'allineamento e del livellamento, gli strumenti e le attrezzature necessarie e una guida passo passo per il processo di allineamento e livellamento.UN. Importanza dell'allineamento e del livellamento
- Accuratezza e precisione: L'allineamento e il livellamento sono essenziali per raggiungere l'elevato grado di accuratezza e precisione richiesti nella lavorazione CNC. Disallineamenti o irregolarità possono portare a errori dimensionali nei pezzi finiti.
- Usura ridotta: Un corretto allineamento riduce lo stress inutile sui componenti della macchina, come ad esempio cuscinettose guide. Ciò prolunga la durata della macchina e riduce i costi di manutenzione.
- Vibrazioni ridotte al minimo: Una macchina ben allineata e livellata genera meno vibrazioni, con conseguenti migliori finiture superficiali e ridotta usura degli utensili. Le vibrazioni possono anche influenzare la longevità dei componenti elettronici sensibili.
- Sicurezza: Le macchine disallineate o non livellate possono rappresentare rischi per la sicurezza. Ad esempio, una macchina non livellata potrebbe ribaltarsi o muoversi inaspettatamente durante il funzionamento.
B. Strumenti e attrezzature necessarie
Per eseguire correttamente l'allineamento e il livellamento, saranno necessari i seguenti strumenti e attrezzature:- Livelli di precisione: Livelli di precisione di alta qualità sono fondamentali per misurare con precisione l'allineamento e il livellamento della macchina.
- Strumenti di regolazione: A seconda del design della tua macchina, potresti aver bisogno di strumenti specifici come chiavi, spessori o viti di regolazione.
- Indicatori del quadrante: Gli indicatori a quadrante aiutano a misurare l'allineamento di vari componenti della macchina, inclusi il mandrino utensile e il piano di lavoro.
- Spessimetri: Gli spessimetri vengono utilizzati per misurare gli spazi e le distanze tra i componenti della macchina durante l'allineamento.
- Laser di allineamento: Un laser di allineamento può essere utile per valutare la rettilineità delle guide e di altri componenti lineari.
C. Processo di allineamento e livellamento passo dopo passo
Segui questi passaggi per allineare e livellare la tua macchina CNC:Passaggio 1: preparare l'area di lavoro
Assicurarsi che l'area di lavoro sia pulita, priva di detriti e ben illuminata. Eliminare eventuali ostacoli che potrebbero ostacolare il processo di allineamento e livellamento.Fase 2: definizione del punto di riferimento
Selezionare un punto di riferimento stabile sul telaio o sulla base della macchina, solitamente fornito dal produttore. Questo punto servirà come riferimento iniziale per tutte le misurazioni.Passaggio 3: livellare la macchina
- Posiziona livelle di precisione su varie superfici della macchina, come base, colonne e piano di lavoro.
- Regolare le viti o gli spessori di livellamento secondo necessità per ottenere un perfetto allineamento orizzontale. Controlla la precisione degli indicatori di bolla sui livelli.
Passaggio 4: allineamento delle guide e delle slitte
- Utilizza comparatori e laser di allineamento per controllare la rettilineità e il parallelismo di guide, slitte e altri componenti lineari.
- Regolare i componenti appropriati per correggere eventuali disallineamenti rilevati.
Passaggio 5: allineamento del mandrino
- Montare un comparatore sul mandrino o sul portautensile della macchina.
- Ruotare il mandrino per verificare l'eccentricità e la concentricità. Regolare il mandrino secondo necessità per ridurre al minimo il runout.
Passaggio 6: allineamento del piano di lavoro
- Controllare l'allineamento del piano di lavoro o dell'attrezzatura di bloccaggio utilizzando i comparatori.
- Regolare il posizionamento del piano di lavoro per garantire che sia perpendicolare agli assi della macchina.
- Dopo le regolazioni, ricontrollare tutti gli allineamenti per garantire che soddisfino le tolleranze specificate.
- Effettuare dei test per verificare che la macchina funzioni accuratamente e produca i risultati desiderati.
Passaggio 8: documentazione
Conservare registrazioni dettagliate del processo di allineamento e livellamento, comprese le misurazioni, le regolazioni apportate e qualsiasi problema riscontrato. Questa documentazione sarà preziosa per riferimenti e manutenzioni future.Passaggio 9: ispezione finale e certificazione
Valuta la possibilità di far eseguire a un tecnico o un ingegnere qualificato un'ispezione finale e una certificazione per garantire che la macchina CNC soddisfi gli standard di settore e i requisiti di sicurezza. Il corretto allineamento e livellamento sono essenziali per il funzionamento affidabile e accurato della tua macchina CNC. Prenditi il tuo tempo durante questo processo, poiché la precisione è fondamentale. Seguendo questi passaggi e utilizzando gli strumenti giusti, puoi garantire che la tua macchina sia in condizioni ottimali per operazioni di lavorazione di successo. Nel prossimo capitolo esploreremo i requisiti di cablaggio elettrico per la tua macchina CNC.Capitolo 5: Cablaggio elettrico
In questo capitolo approfondiremo gli aspetti del cablaggio elettrico dell'installazione della macchina CNC. Un corretto cablaggio elettrico è fondamentale per il funzionamento sicuro ed efficiente della macchina. Questo capitolo tratta la comprensione degli impianti elettrici, il cablaggio della macchina CNC e importanti precauzioni di sicurezza.UN. Comprendere i sistemi elettrici
- Alimentazione: Le macchine CNC richiedono un'alimentazione stabile e adeguata. Comprendere i requisiti di tensione, frequenza e fase specificati dal produttore della macchina. Assicurarsi che l'alimentazione elettrica sia affidabile e abbia una capacità adeguata per gestire il carico elettrico della macchina.
- Pannello elettrico: La maggior parte delle macchine CNC dispone di un quadro elettrico che ospita vari componenti, tra cui interruttori automatici, relè, contattori e morsettiere. Acquisire familiarità con i componenti del pannello e le loro funzioni.
- Schema elettrico: Esaminare gli schemi elettrici forniti dal produttore della macchina. Questi schemi illustrano i collegamenti tra i componenti e sono essenziali per un corretto cablaggio.
- Messa a terra: Una corretta messa a terra è fondamentale per la sicurezza. Assicurarsi che la macchina e l'impianto elettrico siano collegati a terra secondo le normative elettriche locali e le raccomandazioni del produttore.
B. Cablaggio della macchina CNC
Segui questi passaggi per cablare la tua macchina CNC:Passaggio 1: spegnere
Assicurarsi che la macchina e la fonte di alimentazione siano spente prima di iniziare qualsiasi lavoro di cablaggio. Scollegare la macchina dalla fonte di alimentazione.Passaggio 2: piano di cablaggio
Creare uno schema elettrico basato sugli schemi elettrici del produttore. Identificare i componenti, come motori, sensori, interruttori e pannello di controllo, e determinarne le interconnessioni.Passaggio 3: selezione del cavo
Utilizzare cavi e fili adeguati che soddisfino i requisiti di tensione e corrente della macchina. Assicurarsi che i cavi siano della sezione e del tipo di isolamento corretti.Passaggio 4: instradamento dei cavi
Instradare con attenzione i cavi e i fili lungo le canaline o i condotti della macchina. Tenerli organizzati e separati dai componenti in movimento per evitare danni.Passaggio 5: connessioni terminali
Collegare i cavi ai terminali appropriati su componenti come motori, sensori e interruttori. Garantire connessioni sicure crimpando o saldando secondo necessità. Utilizzare le etichette dei cavi per una facile identificazione.Passaggio 6: cablaggio del pannello di controllo
All'interno del quadro elettrico collegare i cavi alle rispettive morsettiere, interruttori automatici, contattori e relè come specificato negli schemi elettrici. Sii meticoloso nel tuo lavoro per evitare collegamenti incrociati o cavi allentati.Passaggio 7: collegamento all'alimentazione
Collegare la macchina alla rete elettrica seguendo le indicazioni del produttore. Ricontrolla le impostazioni di tensione, fase e frequenza per assicurarti che corrispondano ai requisiti della macchina.Passaggio 8: misure di sicurezza
Implementare funzionalità di sicurezza come interruttori di arresto di emergenza e interblocchi di sicurezza, se necessario. Assicurarsi che questi dispositivi di sicurezza siano cablati correttamente e testati per la funzionalità.Passo 9: test
Prima di chiudere il quadro comandi e dare tensione alla macchina, eseguire un test di continuità per verificare eventuali guasti o cortocircuiti nel cablaggio. Assicurarsi che tutti i collegamenti siano sicuri e privi di fili allentati.C. Misure di sicurezza
- Blocco/Tagout (LOTO): Implementare le procedure LOTO per prevenire l'avvio accidentale della macchina durante le attività di cablaggio o manutenzione. I dispositivi di blocco dovrebbero essere utilizzati per isolare le fonti di alimentazione.
- Elettricista qualificato: Gli interventi elettrici devono essere eseguiti da un elettricista o da un tecnico qualificato che conosca i requisiti elettrici della macchina e le normative elettriche locali.
- Protezione da sovraccarico: Installare dispositivi di protezione da sovraccarico adeguati, come interruttori automatici o fusibili, per prevenire danni in caso di guasti elettrici.
- Messa a terra: Assicurarsi che la macchina e tutti i componenti elettrici siano adeguatamente messi a terra per evitare rischi elettrici.
- etichettatura: Etichettare chiaramente tutti i fili, i cavi e i componenti per facilitare la risoluzione dei problemi e la manutenzione futura.
- Ispezioni regolari: Ispezionare periodicamente l'impianto elettrico per rilevare eventuali segni di usura, danni o collegamenti allentati. Affronta tempestivamente eventuali problemi.
- Procedure di emergenza: Stabilire e comunicare procedure di emergenza per problemi elettrici, inclusi incendi elettrici o incidenti dovuti a scosse elettriche.
Capitolo 6: Installazione del software di controllo
In questo capitolo esploreremo il processo di installazione del software di controllo per la tua macchina CNC. Il software di controllo è il cervello del tuo sistema CNC, responsabile dell'interpretazione e dell'esecuzione delle istruzioni di lavorazione. Questo capitolo tratta una panoramica del software di controllo della macchina CNC, una guida passo passo per l'installazione del software e le procedure di calibrazione e test.UN. Panoramica del software di controllo della macchina CNC
- Ruolo del software di controllo: Il software di controllo della macchina CNC è responsabile della traduzione dei dati di progettazione e percorso utensile dal software CAD/CAM in movimenti specifici della macchina. Genera i codici G e i codici M che comandano i motori e gli attuatori della macchina.
- Tipi di software di controllo: Esistono vari tipi di software di controllo CNC, che vanno dal software proprietario fornito dai produttori di macchine alle soluzioni open source e di terze parti. Scegli il software adatto alle esigenze della tua macchina e alla tua familiarità con la sua interfaccia.
- Caratteristiche: Il software di controllo può variare in termini di caratteristiche e capacità. Cerca un software che offra le funzionalità necessarie per le tue specifiche esigenze di lavorazione, come la generazione del percorso utensile, il cambio utensile e il controllo della velocità del mandrino.
B. Installazione del software passo dopo passo
Segui questi passaggi per installare il software di controllo per la tua macchina CNC:Passaggio 1: requisiti di sistema
Verificare i requisiti di sistema specificati dal produttore del software di controllo. Assicurati che il tuo computer soddisfi questi requisiti in termini di hardware, sistema operativo e memoria disponibile.Passaggio 2: download del software o supporto di installazione
Ottieni il software di controllo scaricandolo dal sito Web del produttore o utilizzando il supporto di installazione fornito dal produttore.Passo 3: installazione
- Fare doppio clic sul file di installazione del software per avviare il processo di installazione.
- Seguire le istruzioni visualizzate sullo schermo fornite dal programma di installazione. Ciò può includere la selezione delle directory di installazione, l'accettazione dei contratti di licenza e la configurazione delle impostazioni del software.
- Assicurarsi che l'installazione abbia esito positivo e che non vengano rilevati errori.
Passaggio 4: licenza e attivazione
Se il software di controllo richiede licenza o attivazione, seguire le linee guida del produttore per completare questo processo. Assicurati di disporre delle chiavi di licenza o dei codici di attivazione necessari.Passaggio 5: configurazione della macchina
Configura il software di controllo in modo che corrisponda alle specifiche della tua macchina CNC. Ciò può comportare l'impostazione di parametri per gli assi della macchina, i tipi di motore e altri componenti hardware.Passaggio 6: database di strumenti e materiali
Crea o importa un database di strumenti e materiali nel software di controllo. Queste informazioni sono cruciali per la generazione del percorso utensile e la selezione dei parametri di lavorazione appropriati.C. Calibrazione e test
Dopo aver installato il software di controllo, attenersi alla seguente procedura per la calibrazione e il test:Passaggio 1: impostazione dell'homing e del punto di riferimento
- Home della macchina spostando tutti gli assi nelle rispettive posizioni di riferimento o home. Ciò stabilisce un punto di partenza noto per i movimenti della macchina.
- Verificare che la macchina ritorni accuratamente alla posizione di riferimento.
Passaggio 2: calibrazione dello strumento
- Calibrare la lunghezza e il diametro dell'utensile. Ciò garantisce che la macchina conosca le dimensioni esatte degli strumenti che utilizzerà.
- Eseguire tagli di prova o routine di ritocco dell'utensile per convalidare la calibrazione dell'utensile.
Passaggio 3: impostazione del pezzo
- Fissare un pezzo o un materiale di prova sul piano di lavoro o sul sistema di bloccaggio della macchina.
- Assicurarsi che il pezzo sia correttamente allineato e fissato.
Passaggio 4: esecuzioni di prova
- Caricare un semplice programma di test nel software di controllo.
- Eseguire il programma di test per osservare i movimenti della macchina e i risultati della lavorazione.
- Verifica eventuali problemi quali movimenti imprevisti, collisioni degli strumenti o imprecisioni.
Passaggio 5: messa a punto
Se durante il test vengono identificati problemi, ottimizzare le impostazioni del software di controllo, gli offset degli utensili o la configurazione del pezzo in lavorazione secondo necessità. Ripetere i test finché la macchina non funziona in modo accurato e affidabile.Passaggio 6: documentazione
Documentare tutti i risultati di calibrazione e test, comprese eventuali modifiche apportate al software di controllo. Questa documentazione è preziosa per riferimento futuro e risoluzione dei problemi. L'installazione del software di controllo è un passaggio cruciale nel processo di configurazione della macchina CNC. Seguendo le istruzioni del produttore, calibrando la macchina ed eseguendo test approfonditi, puoi garantire che la tua macchina CNC sia pronta per la produzione e in grado di produrre risultati precisi e accurati. Nel prossimo capitolo esploreremo l'importanza della lubrificazione e della manutenzione per mantenere le prestazioni e la longevità della vostra macchina CNC.Capitolo 7: Lubrificazione e Manutenzione
In questo capitolo ci concentreremo sugli aspetti critici della lubrificazione e della manutenzione della vostra macchina CNC. Una corretta lubrificazione e una manutenzione regolare sono essenziali per garantire la longevità, la precisione e l'affidabilità delle vostre apparecchiature CNC. Tratteremo l'importanza della lubrificazione, dei punti di lubrificazione e la definizione di un programma di manutenzione.UN. Perché la lubrificazione è importante
La lubrificazione gioca un ruolo vitale nelle prestazioni e nella longevità della tua macchina CNC per diversi motivi:- Riduzione dell'attrito: La lubrificazione riduce l'attrito tra le parti mobili, come cuscinetti, guide e viti a ricircolo di sfere. Ciò riduce al minimo l'usura dei componenti, prolungandone la durata.
- Dissipazione di calore: I lubrificanti dissipano il calore generato durante la lavorazione, prevenendo il surriscaldamento dei componenti critici. Ciò aiuta a mantenere la precisione dimensionale e riduce il rischio di dilatazione termica.
- Operazione liscia: Una corretta lubrificazione garantisce movimenti più fluidi e precisi dei componenti della macchina. Ciò è essenziale per ottenere l’elevata precisione richiesta nella lavorazione CNC.
- Prevenire la corrosione: I lubrificanti forniscono una barriera protettiva contro umidità e contaminanti, riducendo il rischio di corrosione sulle superfici metalliche.
- Riduzione del rumore: La lubrificazione può ridurre il rumore generato durante il funzionamento della macchina, creando un ambiente di lavoro più silenzioso e confortevole.
B. Punti di lubrificazione
Diverse macchine CNC hanno diversi punti di lubrificazione che richiedono attenzione. Ecco alcuni punti comuni di lubrificazione da considerare:- Guide lineari: Applicare lubrificante alle guide lineari, che facilitano il movimento degli assi della macchina. Questi possono includere viti a ricircolo di sfere, cuscinetti lineari e guide di scorrimento.
- Cuscinetti mandrino: Lubrificare i cuscinetti del mandrino per garantire una rotazione regolare e ridurre l'attrito durante le operazioni di taglio o lavorazione.
- Meccanismo di cambio utensile: Se la tua macchina è dotata di cambio utensile automatico, assicurati che le parti mobili del meccanismo siano adeguatamente lubrificate per evitare inceppamenti o malfunzionamenti.
- Riduttori: I riduttori, se presenti nella macchina, potrebbero richiedere lubrificazione a intervalli specificati per mantenerne l'efficienza e ridurre l'usura.
- Viti a ricircolo di sfere: Le viti a ricircolo di sfere sono componenti cruciali nelle macchine CNC. Una corretta lubrificazione delle viti a ricircolo di sfere e dei componenti associati è essenziale per un posizionamento e un movimento accurati.
- Pompa di raffreddamento: Se la macchina utilizza un sistema di raffreddamento, assicurarsi che la pompa sia adeguatamente lubrificata e che il liquido di raffreddamento sia pulito e privo di contaminanti.
- Motori degli assi: A seconda del tipo di motori utilizzati per il movimento dell'asse (ad esempio, passo-passo o servo), seguire le raccomandazioni del produttore per la lubrificazione o la manutenzione.
- Guarnizioni e Guarnizioni: Ispezionare e sostituire guarnizioni e guarnizioni usurate o danneggiate secondo necessità per evitare perdite di lubrificante e contaminazione.
C. Programma di manutenzione
Stabilire un programma di manutenzione regolare è essenziale per mantenere la macchina CNC in condizioni ottimali. Ecco i passaggi per creare un programma di manutenzione:Passaggio 1: linee guida del produttore
Consultare la documentazione e le raccomandazioni del produttore per gli intervalli di manutenzione, i tipi di lubrificazione e le procedure specifiche.Passaggio 2: manutenzione quotidiana
Implementare routine di manutenzione quotidiana che includano attività come la rimozione dei detriti, il controllo degli elementi di fissaggio allentati e l'ispezione dei livelli del liquido di raffreddamento. Queste attività aiutano a prevenire l'escalation di problemi minori.Passaggio 3: manutenzione settimanale o mensile
Pianifica attività di manutenzione più approfondite su base settimanale o mensile, a seconda dell'utilizzo della macchina. Ciò può comportare una pulizia approfondita, lubrificazione e ispezione dei componenti critici.Passaggio 4: manutenzione trimestrale o semestrale
Eseguire attività di manutenzione più estese, come il controllo e la regolazione dell'allineamento, l'ispezione dei collegamenti elettrici e la sostituzione di parti usurate o danneggiate.Passaggio 5: manutenzione annuale
Annualmente, prendere in considerazione un'ispezione completa da parte di un tecnico o ingegnere qualificato. Ciò dovrebbe includere un ciclo di lubrificazione completo, controlli di calibrazione ed eventuali riparazioni o sostituzioni necessarie.Passaggio 6: documentazione
Mantenere registrazioni dettagliate di tutte le attività di manutenzione, comprese le date, le attività eseguite e qualsiasi problema identificato. Questa documentazione è preziosa per tenere traccia della storia della macchina e pianificare la manutenzione futura.Passaggio 7: formazione
Assicurarsi che il personale responsabile della manutenzione sia adeguatamente formato e abbia accesso agli strumenti e alle risorse necessarie. La lubrificazione e la manutenzione regolari sono essenziali per massimizzare la durata e le prestazioni della vostra macchina CNC. Seguendo un programma di manutenzione ben stabilito e affrontando i punti di lubrificazione, è possibile prevenire l'usura prematura e garantire che la macchina continui a produrre pezzi accurati e di alta qualità. Nel prossimo capitolo discuteremo delle procedure di sicurezza e delle linee guida per il funzionamento della macchina CNC.Capitolo 8: Procedure di sicurezza per macchine CNC
La sicurezza è di fondamentale importanza quando si lavora con macchine CNC. In questo capitolo esploreremo le principali procedure di sicurezza e linee guida per il funzionamento delle macchine CNC, inclusa la sicurezza delle macchine CNC, le procedure di arresto di emergenza e l'uso di dispositivi di protezione individuale (DPI).UN. Sicurezza delle macchine CNC
- Formazione: Assicurarsi che tutto il personale che opera o lavora attorno alle macchine CNC abbia ricevuto una formazione completa sulla sicurezza. Ciò dovrebbe includere formazione specifica per la macchina, procedure operative sicure e riconoscimento dei pericoli.
- Protezioni macchina: Mantenere tutte le protezioni della macchina e gli interblocchi di sicurezza in posizione e funzionanti correttamente. Queste caratteristiche di sicurezza sono progettate per proteggere gli operatori dalle parti in movimento e dai potenziali pericoli.
- Etichette di sicurezza: Assicurarsi che le etichette di sicurezza e i segnali di avvertenza siano ben visibili sulla macchina. Queste etichette forniscono informazioni essenziali sui potenziali pericoli e sulle precauzioni di sicurezza.
- Arresto di emergenza: Familiarizzare gli operatori con la posizione e l'uso del pulsante di arresto di emergenza. Assicurati che sia facilmente accessibile in caso di emergenza.
- Cancella area di lavoro: Mantenere uno spazio di lavoro privo di ingombri attorno alla macchina CNC. Rimuovere eventuali strumenti, materiali o detriti non necessari che potrebbero rappresentare un pericolo di inciampo o interferire con il funzionamento della macchina.
- Blocco/Tagout della macchina (LOTO): Implementare procedure di blocco/tagout per togliere tensione e proteggere la macchina prima di eseguire interventi di manutenzione o riparazione. I dispositivi di blocco impediscono l'avvio accidentale della macchina.
- Sicurezza del mandrino e dell'utensile: Maneggiare gli utensili da taglio e i cambi utensile con cura. Assicurarsi che gli strumenti siano adeguatamente fissati nei portautensili e che i cambi degli strumenti vengano eseguiti seguendo procedure sicure.
- Manipolazione del materiale: Utilizzare attrezzature e tecniche di sollevamento adeguate durante la movimentazione di materiali o pezzi pesanti. Evitare di sovraccaricare la capacità di peso della macchina.
- Sicurezza antincendio: Tenere gli estintori e i rilevatori di fumo nelle vicinanze. Sviluppare e comunicare protocolli di sicurezza antincendio, inclusa l'ubicazione delle uscite antincendio e le procedure di evacuazione.
B. Procedure di arresto di emergenza
- Pulsante di arresto di emergenza: In caso di emergenza o quando è necessario lo spegnimento immediato, premere il pulsante di arresto di emergenza. Questo pulsante è generalmente grande, rosso e facilmente accessibile.
- Arresta tutti i movimenti: Il pulsante di arresto di emergenza dovrebbe arrestare tutti i movimenti della macchina e interrompere l'alimentazione alla macchina. Assicurarsi che la macchina si arresti completamente.
- Blocco/tagout: Dopo aver utilizzato il pulsante di arresto di emergenza, seguire le procedure di blocco/tagout per proteggere la macchina ed evitare riavvii accidentali.
- Avvisare le autorità: Se si verifica un incidente o una situazione pericolosa, contattare le autorità competenti, come il personale di manutenzione o i supervisori, per risolvere il problema e garantire che la macchina possa funzionare nuovamente in sicurezza.
C. Dispositivi di Protezione Individuale (DPI)
- Occhiali di sicurezza: Gli operatori e il personale nelle vicinanze della macchina CNC devono indossare occhiali di sicurezza con adeguata resistenza agli urti per proteggere gli occhi dai detriti volanti.
- Protezione dell'udito: Nelle officine meccaniche rumorose, è necessario indossare protezioni per l'udito, come tappi per le orecchie o cuffie antirumore, per prevenire danni all'udito.
- Guanti: Quando si maneggiano materiali o si eseguono attività di manutenzione, indossare guanti adeguati al lavoro. Assicurarsi che i guanti non costituiscano un pericolo in prossimità delle parti mobili della macchina.
- Protezione respiratoria: If materiale di lavoraziones generano polvere o fumi, utilizzare dispositivi di protezione respiratoria, come maschere antipolvere o respiratori, per proteggersi dai rischi di inalazione.
- Scarpe antinfortunistiche: Indossare scarpe o stivali antinfortunistici robusti con suola antiscivolo per proteggersi da lesioni ai piedi e garantire una buona trazione nell'area di lavoro.
- Indumenti protettivi: A seconda del processo di lavorazione e dei materiali utilizzati, indossare indumenti protettivi adeguati, come grembiuli o tute integrali.
- Caschi di sicurezza: Negli ambienti in cui vi è rischio di caduta di oggetti, indossare elmetti di sicurezza o elmetti di protezione per la protezione della testa.
- Visiere: Per le attività che comportano potenziali rischi per il viso, come spruzzi di refrigerante o trucioli, utilizzare visiere oltre agli occhiali di sicurezza.
Capitolo 9: Risoluzione dei problemi comuni di installazione
In questo capitolo esploreremo i problemi comuni che possono sorgere durante l'installazione di macchine CNC e forniremo soluzioni per risolvere questi problemi. Inoltre, discuteremo delle tecniche di risoluzione dei problemi che possono aiutarti a identificare e risolvere i problemi in modo efficace.UN. Problemi comuni e soluzioni
-
Problemi elettrici:
- Problema: La macchina CNC non si accende.
- Soluzione: Controllare la fonte di alimentazione, i collegamenti elettrici e i fusibili. Assicurarsi che il pulsante di arresto di emergenza sia rilasciato.
-
Disallineamento meccanico:
- Problema: La macchina produce tagli o dimensioni del pezzo imprecisi.
- Soluzione: Riallineare e livellare la macchina. Verificare la presenza di componenti allentati o guide usurate e sostituirli se necessario.
-
Vibrazioni o vibrazioni dell'utensile:
- Problema: La macchina produce vibrazioni o vibrazioni dell'utensile, che influiscono sulla finitura superficiale.
- Soluzione: Controllare che il portautensili e la pinza del mandrino siano posizionati correttamente. Regola i parametri di taglio e le impostazioni del percorso utensile.
-
Errori di comunicazione:
- Problema: Il controller CNC non può comunicare con il computer o il software CAD/CAM.
- Soluzione: Verificare le connessioni dei cavi, le velocità di trasmissione e le impostazioni sia sulla macchina che sul computer. Garantire la corretta installazione di software e driver.
-
Rottura dell'utensile:
- Problema: Gli utensili si rompono spesso durante la lavorazione.
- Soluzione: Controllare l'allineamento dell'utensile, le condizioni del portautensile e l'eccentricità del mandrino. Regolare avanzamenti e velocità in base al materiale dell'utensile e al pezzo da lavorare.
-
Problemi di refrigerante o lubrificazione:
- Problema: Flusso di refrigerante/lubrificazione insufficiente o irregolare.
- Soluzione: Controllare i componenti del sistema di raffreddamento e lubrificazione, come pompe, tubi flessibili e ugelli. Pulire o sostituire i filtri e garantire livelli di fluido adeguati.
-
Errori software:
- Problema: Il software di controllo visualizza messaggi di errore o comportamenti imprevisti.
- Soluzione: Esaminare i messaggi di errore e consultare la documentazione del software. Verifica eventuali problemi di compatibilità e aggiorna il software o il firmware secondo necessità.
B. Tecniche di risoluzione dei problemi
- Approccio sistematico: Durante la risoluzione dei problemi, adottare un approccio sistematico identificando e isolando la fonte del problema. Iniziare con i controlli più semplici e indagare progressivamente le cause più complesse.
- Documentazione: Fare riferimento ai manuali della macchina, alla documentazione e alle risorse fornite dal produttore per indicazioni sulla risoluzione dei problemi e interpretazioni dei codici di errore.
- Misurazione e test: Utilizzare strumenti di misura come comparatori, calibri e micrometri per valutare l'allineamento, le dimensioni e il runout dell'utensile. Effettuare tagli di prova per verificare la precisione della lavorazione.
- Ispezione visuale: Effettuare un'ispezione visiva approfondita della macchina, verificando la presenza di elementi di fissaggio allentati, componenti danneggiati o segni visibili di usura.
- Registri e registrazioni: Esaminare i registri di manutenzione, i registri degli errori e i record dei problemi passati per identificare problemi o modelli ricorrenti.
- Consulta gli esperti: Se riscontri problemi complessi o persistenti, consulta esperti, come il supporto tecnico del produttore, tecnici qualificati o macchinisti esperti che potrebbero aver riscontrato problemi simili.
- Risoluzione dei problemi sicuri: Garantire sempre la sicurezza durante la risoluzione dei problemi. Seguire le procedure di blocco/tagout, spegnere la macchina e utilizzare dispositivi di protezione individuale (DPI) adeguati.
- Documentazione: Conservare registrazioni dettagliate delle attività di risoluzione dei problemi, comprese le misure adottate, le osservazioni e le soluzioni applicate. Questi record possono essere preziosi per riferimento futuro.
- Apprendimento continuo: Incoraggia una cultura di apprendimento continuo e di condivisione delle conoscenze all'interno del tuo team. L'esperienza acquisita dalla risoluzione dei problemi può portare a migliori pratiche di manutenzione preventiva.
Capitolo 10: Verifiche finali e test
In questo capitolo conclusivo, discuteremo i passaggi essenziali per eseguire programmi di test, garantire la precisione e mettere a punto l'installazione della macchina CNC per ottenere prestazioni ottimali.UN. Esecuzione di programmi di test
- Selezione dei programmi di test: Prepara programmi di test che comprendono una gamma di operazioni di lavorazione che la tua macchina CNC eseguirà. Questi programmi dovrebbero includere movimenti di base, cambi di utensile e vari scenari di taglio.
- Configurazione dell'utensile e del pezzo: Montare gli strumenti appropriati e fissare un pezzo di prova sul piano di lavoro o sull'attrezzatura della macchina. Assicurarsi che gli offset utensile e gli offset pezzo siano programmati correttamente.
- Funzionamento a secco: Inizialmente, eseguire un ciclo di prova senza effettuare alcun taglio. Ciò consente di controllare i movimenti della macchina, i cambi utensile e il flusso complessivo del programma per eventuali errori o comportamenti imprevisti.
- Selezione del materiale: Scegli un materiale di prova simile a quello che prevedi di utilizzare per i tuoi progetti di lavorazione reali. Ciò garantisce che i risultati del test imitino fedelmente le condizioni del mondo reale.
- Prove di taglio: Eseguire i programmi di prova con operazioni di taglio. Monitora le prestazioni della macchina, prestando molta attenzione alla precisione del percorso utensile, alla velocità del mandrino e alle velocità di avanzamento.
B. Garantire la precisione
- Misurazione e ispezione: Dopo aver eseguito i programmi di prova, misurare le dimensioni e la finitura superficiale dei pezzi di prova utilizzando strumenti di misura di precisione. Confrontare i risultati con le specifiche di progettazione previste.
- Ispezione dello strumento: Ispezionare gli utensili da taglio per rilevare eventuali segni di usura, come bordi scheggiati o usura eccessiva dell'utensile. Sostituisci o riaffila gli strumenti secondo necessità.
- Ispezione del pezzo: Esaminare il pezzo di prova per eventuali difetti, problemi di finitura superficiale o deviazioni dalla geometria desiderata. Affrontare eventuali problemi identificati durante l'ispezione.
- Feedback e analisi: Analizzare i risultati del test per identificare eventuali discrepanze o deviazioni rispetto ai risultati attesi. Determinare se sono necessarie modifiche per migliorare la precisione.
C. Ritocchi
- Ottimizzazione del percorso utensile: Se i risultati dei test rivelano imprecisioni o problemi di finitura superficiale, valuta la possibilità di ottimizzare i percorsi utensile nel software CAM. Regola i parametri del percorso utensile, la selezione dell'utensile, le velocità di taglio e gli avanzamenti secondo necessità.
- Regolazioni dei parametri della macchina: Consultare la documentazione della macchina per ottimizzare parametri specifici, come accelerazione, decelerazione e compensazione del gioco. Queste regolazioni possono migliorare la precisione.
- Calibrazione offset utensile: Se necessario, ricalibrare gli offset utensile. Garantire che la macchina compensi accuratamente la lunghezza e il diametro dell'utensile, riducendo gli errori nella lavorazione.
- Correzione dell'offset pezzo: Controllare e correggere gli offset pezzo per garantire che la macchina posizioni l'utensile esattamente rispetto al pezzo. Piccoli errori nell'offset pezzo possono portare a significative imprecisioni.
- Nuovo test: Dopo aver apportato modifiche e perfezionamenti, eseguire nuovamente i programmi di test per verificare i miglioramenti in termini di precisione e finitura superficiale.
- Documentazione: Documentare tutte le attività di perfezionamento, le regolazioni e i risultati dei test per riferimento futuro. Questa documentazione sarà preziosa per mantenere la coerenza nelle operazioni di lavorazione.
Capitolo 11: Formazione e sviluppo delle competenze
In questo capitolo sottolineeremo l’importanza della formazione e dello sviluppo delle competenze sia per gli operatori delle macchine che per il personale di manutenzione. Una formazione adeguata e il miglioramento delle competenze sono fondamentali per garantire un funzionamento sicuro ed efficiente della macchina CNC, nonché per una manutenzione e una risoluzione dei problemi efficaci dell'attrezzatura.UN. Formazione degli operatori
- Funzionamento di base della macchina: Gli operatori dovrebbero ricevere una formazione completa sugli aspetti fondamentali del funzionamento della macchina CNC, inclusi l'avvio, l'arresto, l'homing e il jogging della macchina.
- Comprensione dei codici G e dei codici M: Gli operatori devono essere esperti nell'interpretazione e nella modifica dei codici G e M, che controllano i movimenti e le funzioni della macchina.
- Gestione degli strumenti: Le corrette tecniche di gestione degli utensili, compresi il cambio degli utensili, gli offset degli utensili e la calibrazione degli utensili, sono essenziali per prevenire incidenti e garantire la precisione della lavorazione.
- Impostazione del pezzo: La formazione dovrebbe riguardare l'impostazione del pezzo, compreso il bloccaggio del pezzo, il caricamento del materiale e il fissaggio dei pezzi al piano di lavoro o all'attrezzatura della macchina.
- Procedure di sicurezza: Gli operatori devono essere esperti nelle procedure di sicurezza delle macchine CNC, nei protocolli di arresto di emergenza e nell'uso dei dispositivi di protezione individuale (DPI).
- Nozioni di base sulla risoluzione dei problemi: Le competenze di base per la risoluzione dei problemi, come identificare problemi comuni e sapere quando chiedere assistenza, possono aiutare gli operatori ad affrontare tempestivamente problemi minori.
- Controllo di qualità: La formazione sulle tecniche di controllo e ispezione della qualità è fondamentale per garantire che i pezzi finiti soddisfino le tolleranze specificate e i requisiti di finitura superficiale.
- Simulazione e pratica: Gli operatori dovrebbero avere l'opportunità di fare pratica pratica ed esercizi di simulazione per migliorare le proprie capacità e acquisire sicurezza nell'utilizzo della macchina CNC.
B. Formazione sulla manutenzione
- Manutenzione preventiva: Il personale addetto alla manutenzione deve ricevere una formazione sulle attività di manutenzione preventiva di routine specifiche della macchina CNC, comprese le routine di lubrificazione, pulizia e ispezione.
- Componenti della macchina: Una conoscenza approfondita dei componenti della macchina, inclusi motori, sensori, azionamenti e sistemi elettrici, è necessaria affinché il personale di manutenzione possa diagnosticare e risolvere i problemi in modo efficace.
- Tecniche di risoluzione dei problemi: Competenze avanzate di risoluzione dei problemi, come la diagnosi di problemi elettrici, meccanici e relativi al software, sono essenziali per ridurre al minimo i tempi di fermo e ottimizzare le prestazioni della macchina.
- Lubrificazione e gestione dei fluidi: La corretta conoscenza dei punti di lubrificazione, dei tipi di fluido e dei sistemi di filtraggio è fondamentale per mantenere l'integrità meccanica della macchina.
- Impianti Elettrici: Il personale di manutenzione deve essere addestrato sui sistemi elettrici, compresa la comprensione degli schemi elettrici, dei protocolli di sicurezza elettrica e della sostituzione dei componenti elettrici.
- Calibrazione avanzata: La formazione su tecniche di calibrazione avanzate, come l'allineamento laser e la misurazione dell'eccentricità del mandrino, può migliorare la precisione della macchina CNC.
- Aggiornamenti software: La familiarità con gli aggiornamenti software e firmware è importante per mantenere aggiornati il software di controllo e il firmware della macchina.
C. Miglioramento delle abilità
- Apprendimento continuo: Incoraggiare una cultura di apprendimento continuo sia tra gli operatori che tra il personale di manutenzione. Ciò può includere la partecipazione a workshop, seminari e corsi online relativi alla tecnologia CNC.
- Valutazione delle competenze: Valutare periodicamente le competenze e le conoscenze degli operatori e del personale di manutenzione per identificare aree di miglioramento e formazione mirata.
- Formazione incrociata: Considerare la formazione incrociata degli operatori nelle attività di manutenzione di base e viceversa. Ciò può migliorare la comprensione generale e la collaborazione all’interno del team.
- tutoraggio: Implementare programmi di tutoraggio in cui i dipendenti esperti possano fornire indicazioni e condividere le proprie conoscenze con i membri del team meno esperti.
- Risoluzione dei problemi: Incoraggiare i dipendenti a impegnarsi attivamente in esercizi di risoluzione dei problemi e nell’analisi delle cause profonde, promuovendo una cultura di risoluzione proattiva dei problemi.
- Ciclo di feedback: Stabilisci un ciclo di feedback in cui gli operatori e il personale di manutenzione possono comunicare problemi, condividere approfondimenti e suggerire miglioramenti per il funzionamento e la manutenzione della macchina.
Conclusione
In questa guida completa, abbiamo esplorato l'intricato processo di installazione della macchina CNC, coprendo un'ampia gamma di argomenti per garantire che la tua macchina CNC sia assemblata, installata e utilizzata in modo efficace e sicuro. Riassumiamo i punti chiave, sottolineiamo l'importanza di una corretta installazione della macchina CNC e guardiamo al futuro della tecnologia CNC.UN. Riepilogo dei punti chiave
In questa guida abbiamo trattato i seguenti punti chiave:- Comprendere le macchine CNC: Abbiamo iniziato discutendo cosa sono le macchine CNC, i vari tipi disponibili e i loro componenti essenziali.
- Preparazione pre-installazione: Abbiamo sottolineato l'importanza di preparare l'area di lavoro, soddisfare i requisiti elettrici e di alimentazione e implementare misure di sicurezza prima dell'installazione.
- Assemblaggio della macchina CNC: Sono state fornite fasi dettagliate per il disimballaggio, l'organizzazione dei componenti, l'assemblaggio del telaio della macchina, il collegamento di motori e azionamenti, l'installazione del pannello di controllo e la gestione dei cavi.
- Allineamento e livellamento: Abbiamo discusso l'importanza dell'allineamento e del livellamento, gli strumenti necessari e il processo passo passo per ottenere un allineamento preciso.
- Cavi elettrici: Sono stati trattati in modo approfondito la comprensione dei sistemi elettrici, il cablaggio della macchina CNC e l'adesione alle precauzioni di sicurezza durante i lavori elettrici.
- Installazione del software di controllo: Sono state discusse l'installazione del software di controllo, la calibrazione e le procedure di test per garantire il corretto funzionamento della macchina CNC.
- Lubrificazione e Manutenzione: È stata evidenziata l'importanza della lubrificazione e della manutenzione per la longevità e le prestazioni della macchina, compresi i punti di lubrificazione e i programmi di manutenzione.
- Procedure di sicurezza: Le procedure di sicurezza, i protocolli di arresto di emergenza e l'uso dei dispositivi di protezione individuale (DPI) sono stati affrontati per creare un ambiente di lavoro sicuro.
- Risoluzione dei problemi di installazione comuni: Sono stati forniti problemi comuni e tecniche di risoluzione per aiutare a identificare e risolvere i problemi in modo efficace.
- Verifiche finali e collaudi: Sono stati discussi l'esecuzione di programmi di test, la garanzia della precisione e la messa a punto della macchina per ottenere prestazioni ottimali.
- Formazione e sviluppo delle competenze: È stata sottolineata l'importanza della formazione degli operatori e del personale addetto alla manutenzione, nonché del continuo miglioramento delle competenze.
B. L'importanza di una corretta installazione della macchina CNC
La corretta installazione della macchina CNC è la base su cui si costruisce un'operazione di lavorazione di successo. È essenziale per i seguenti motivi:- Precisione: Una macchina CNC ben installata ha maggiori probabilità di produrre parti accurate e precise, riducendo scarti e rilavorazioni.
- Sicurezza: Un'installazione conforme agli standard e alle procedure di sicurezza garantisce il benessere degli operatori della macchina e del personale di manutenzione.
- Longevità: Una corretta installazione e una manutenzione regolare prolungano la vita della tua macchina CNC, proteggendo il tuo investimento.
- Efficienza: Una macchina installata correttamente funziona in modo efficiente, riducendo al minimo i tempi di fermo macchina e massimizzando la produttività.
- Qualità: La qualità dell'installazione influisce direttamente sulla qualità delle parti lavorate, portando a clienti soddisfatti e ad una migliore reputazione.
C. Guardando avanti
Man mano che la tecnologia continua ad avanzare, le macchine CNC diventeranno ancora più capaci e versatili. È essenziale rimanere informati sugli ultimi sviluppi, sugli aggiornamenti software e sulle migliori pratiche nella lavorazione CNC. Inoltre, man mano che la tecnologia CNC diventa più accessibile, sempre più industrie e aziende possono beneficiare dei suoi vantaggi. In conclusione, l’installazione di macchine CNC è un processo complesso ma gratificante. Seguendo le linee guida e le migliori pratiche descritte in questa guida, puoi preparare il terreno per un'operazione di lavorazione CNC di successo. Ricorda che l'apprendimento continuo, la formazione e la manutenzione continua sono fondamentali per mantenere e migliorare le prestazioni delle tue macchine CNC mentre guardi avanti a un futuro pieno di opportunità nel mondo della produzione di precisione.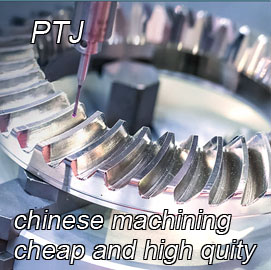
I nostri servizi
- Lavorazione a 5 assi
- Fresatura a controllo numerico
- Tornitura cnc
- Industrie di lavorazione
- Processo di lavorazione
- Trattamento della superficie
- Lavorazione dei metalli
- Lavorazione plastica
- Stampo per metallurgia delle polveri
- Die Casting
- Galleria delle parti
Casi Studio
- Parti metalliche per auto
- Pezzi meccanici
- Dissipatore di calore a LED
- Parti di costruzione
- Parti mobili
- Parti mediche
- Parti elettroniche
- Lavorazione su misura
- Parti di biciclette
Lista materiali
- Lavorazione dell'alluminio
- Lavorazione del titanio
- Lavorazione dell'acciaio inossidabile
- Lavorazione del rame
- Lavorazione dell'ottone
- Lavorazione Super Lega
- Peek lavorazione
- Lavorazione UHMW
- Lavorazione Unilate
- Lavorazione PA6
- Lavorazione PPS
- Lavorazione Teflon
- Lavorazione Inconel
- Lavorazione dell'acciaio per utensili
- Più materiale
Galleria delle parti