Come vengono lavorati i pezzi di alta precisione
2023-09-22
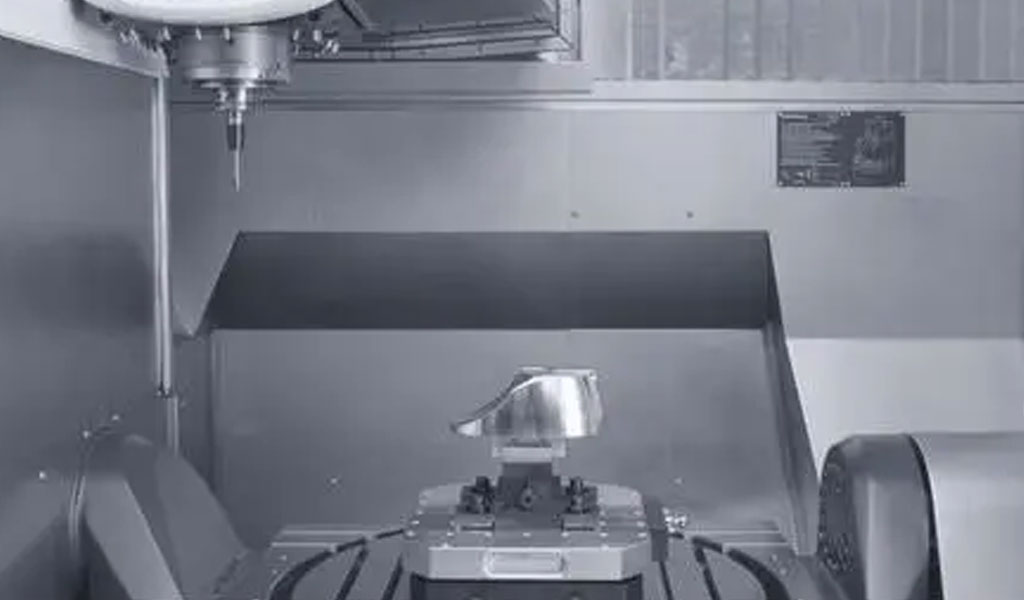
Comprendere la lavorazione meccanica di precisione
La lavorazione meccanica di precisione è una pietra angolare della produzione moderna, responsabile della produzione di componenti complessi e accurati utilizzati in un'ampia gamma di settori. Per coglierne appieno il significato, esploriamo i concetti chiave della lavorazione meccanica di precisione, il suo ruolo vitale in diversi settori e il percorso storico che ha portato al suo attuale stato di eccellenza.A. Cos'è la lavorazione meccanica di precisione?
La lavorazione di precisione si riferisce a una serie di processi di produzione che rimuovono materiale da un pezzo con un elevato grado di precisione e controllo, ottenendo componenti finemente realizzati con tolleranze strette. Questo processo trasforma le materie prime, come metalli, plastica o ceramica, in parti precise che soddisfano specifiche rigorose. Le caratteristiche chiave della lavorazione meccanica di precisione includono:- Precisione: La lavorazione di precisione garantisce che il prodotto finale sia esattamente conforme al progetto previsto, con una deviazione minima.
- Tolleranze strette: Consente la produzione di parti con tolleranze estremamente strette, il che significa che i componenti finiti aderiscono strettamente alle misure specificate.
- Finitura superficiale superiore: La lavorazione di precisione fornisce finiture superficiali eccezionali, spesso eliminando la necessità di ulteriori processi di finitura.
- Geometrie complesse: Può creare forme, contorni e caratteristiche complesse, rendendolo indispensabile nella produzione di componenti con design complessi.
- Ripetibilità: Precisione processo di lavorazioneSono altamente ripetibili e garantiscono una qualità costante su più parti.
- Versatilità: Può essere applicato a un'ampia gamma di materiali, rendendolo adatto a diversi settori.
B. Importanza della lavorazione meccanica di precisione
La lavorazione di precisione riveste un’importanza enorme in diversi settori critici, incidendo su vari aspetti della nostra vita quotidiana. Ecco alcune ragioni convincenti per la sua importanza:- Industria aerospaziale: Nel settore aerospaziale, la lavorazione meccanica di precisione è indispensabile per realizzare componenti che resistano a condizioni estreme. Motori di aerei, atterraggio ingranaggioe gli elementi strutturali si affidano a parti lavorate con precisione per garantire sicurezza e prestazioni.
- Dispositivi medicali: I dispositivi medici come strumenti chirurgici, protesi e dispositivi impiantabili richiedono lavorazioni meccaniche di precisione per la biocompatibilità, l'accuratezza e la sicurezza del paziente.
- Settore automobilistico: I pezzi lavorati con precisione sono essenziali per l'industria automobilistica per garantire l'affidabilità e l'efficienza dei veicoli. Componenti come parti del motore, sistemi di trasmissione e meccanismi di frenatura si basano su una lavorazione precisa.
- Elettronica e semiconduttori: La lavorazione di precisione è fondamentale nella produzione di componenti microelettronici e dispositivi a semiconduttore, dove tolleranze minuscole sono indispensabili per la funzionalità.
- Settore energetico: L'industria energetica fa affidamento sulla lavorazione meccanica di precisione per la produzione di parti critiche utilizzate nella produzione di energia, tra cui turbine, generatori e componenti di trasmissione.
- Costruzione di utensili e stampi: La lavorazione meccanica di precisione è fondamentale nella produzione di utensili e matrici che, a loro volta, vengono utilizzati per creare innumerevoli altri prodotti.
- Elettronica di consumo: La produzione di smartphone, laptop e altri prodotti elettronici di consumo beneficia di lavorazioni meccaniche di precisione per garantire design eleganti e funzionalità ottimali.
- Ricerca e Sviluppo: I ricercatori e gli scienziati dipendono da componenti lavorati con precisione per esperimenti, prototipi e apparecchiature di laboratorio.
C. Prospettiva storica
Il viaggio della lavorazione meccanica di precisione risale alle antiche civiltà, dove abili artigiani utilizzavano strumenti rudimentali per modellare i materiali. Tuttavia, la precisione raggiunta a quei tempi era limitata rispetto agli standard contemporanei.- Prima lavorazione di precisione: La rivoluzione industriale dei secoli XVIII e XIX ha segnato un periodo cruciale nello sviluppo della lavorazione meccanica di precisione. L'invenzione delle macchine utensili, come torni e fresatrici, ha rivoluzionato la produzione consentendo una maggiore precisione e coerenza.
- Seconda Guerra Mondiale: La lavorazione meccanica di precisione ha svolto un ruolo fondamentale durante la seconda guerra mondiale, poiché era essenziale per produrre attrezzature militari con la precisione e l'uniformità richieste. Quest'epoca vide i progressi nelle tecniche di lavorazione e l'emergere di nuovi materiali.
- Progressi del dopoguerra: Il dopoguerra ha visto un'impennata delle innovazioni tecnologiche, compreso l'uso di macchine a controllo numerico computerizzato (CNC). Lavorazione CNC ha consentito operazioni automatizzate ed estremamente precise, inaugurando una nuova era della produzione.
- L'era digitale: L'integrazione di computer e software nei processi di lavorazione ha ulteriormente elevato la precisione della lavorazione. Le moderne macchine CNC possono eseguire operazioni complesse con una precisione senza pari, rendendole indispensabili nel panorama produttivo odierno.
Materiali e loro significato
I materiali sono il fondamento della lavorazione meccanica di precisione e la selezione del materiale giusto gioca un ruolo fondamentale nella produzione di parti di alta precisione. In questa sezione approfondiremo l'importanza di selezionare i materiali appropriati, comprenderemo il significato delle proprietà dei materiali ed esploreremo i vari fattori che influiscono sulla lavorabilità.A. Selezione dei materiali
La scelta dei materiali nella lavorazione di precisione è una decisione fondamentale che incide direttamente sulle prestazioni, sulla durata e sulla funzionalità del prodotto finale. I produttori devono considerare diversi fattori nella scelta dei materiali:- Idoneità materiale: Il materiale deve essere adatto all'applicazione prevista. Diversi settori e applicazioni hanno requisiti diversi, come resistenza alla temperatura, resistenza alla corrosione e conduttività elettrica.
- Proprietà meccaniche: Le proprietà meccaniche come resistenza alla trazione, durezza e duttilità sono cruciali. Ad esempio, nel settore aerospaziale, i materiali con elevata resistenza alla trazione sono preferiti per i componenti strutturali.
- Proprietà termali: Alcune applicazioni richiedono materiali con eccellente conduttività termica o resistenza alle alte temperature. Ciò è particolarmente importante in settori come la produzione di energia e l’elettronica.
- Resistenza alla corrosione: Negli ambienti in cui la corrosione rappresenta un problema, sono preferiti i materiali con elevata resistenza alla corrosione, come l'acciaio inossidabile o il titanio.
- Considerazioni sul peso: Settori come quello automobilistico e aerospaziale spesso danno priorità ai materiali leggeri come i compositi in alluminio o fibra di carbonio per ridurre il consumo di carburante e migliorare le prestazioni.
- Vincoli di costo: Il costo è un fattore significativo nella scelta del materiale. I materiali ad alte prestazioni possono essere costosi, quindi i produttori devono trovare un equilibrio tra prestazioni ed efficienza dei costi.
- Conformità normativa: In settori come quello sanitario, i materiali devono soddisfare rigorosi standard normativi in materia di biocompatibilità e sicurezza.
- Disponibilità: Anche la disponibilità dei materiali e le loro fonti influiscono sulla selezione. Alcune leghe o compositi specializzati potrebbero avere una disponibilità limitata.
B. Proprietà dei materiali
Comprendere le proprietà dei materiali è fondamentale per la lavorazione di precisione. Ecco alcune proprietà chiave dei materiali e il loro significato:- Resistenza alla trazione: La resistenza alla trazione misura la capacità di un materiale di sopportare una forza di trazione senza rompersi. È indispensabile per componenti strutturali e parti sottoposte a sollecitazioni meccaniche.
- Durezza: La durezza indica la resistenza di un materiale alla deformazione e all'usura. I materiali duri sono adatti per gli utensili da taglio, mentre i materiali più morbidi possono essere preferiti per alcune applicazioni, come le guarnizioni.
- duttilità: La duttilità si riferisce alla capacità di un materiale di deformarsi senza rompersi quando sottoposto a sollecitazioni di trazione. I materiali duttili sono più facili da modellare ma potrebbero non essere adatti per applicazioni che richiedono rigidità.
- Conduttività termica: I materiali con elevata conduttività termica dissipano efficacemente il calore. Questa proprietà è vitale nelle applicazioni in cui il controllo della temperatura è fondamentale.
- Conduttività elettrica: La conduttività elettrica è essenziale nei componenti elettronici e elettrici, dove i materiali devono facilitare il flusso di elettricità.
- Proprietà magnetiche: Le proprietà magnetiche sono importanti in settori come l'elettromagnetismo e l'elettronica, dove potrebbe essere necessario che i materiali siano ferromagnetici o non magnetici.
- Resistenza chimica: I materiali devono resistere alla corrosione chimica in ambienti in cui sono esposti ad acidi, basi o altre sostanze corrosive.
C. Fattori di lavorabilità
La lavorabilità si riferisce alla facilità con cui un materiale può essere lavorato, tagliato o modellato. È influenzato da vari fattori, tra cui:- Durezza del materiale: I materiali più morbidi sono generalmente più facili da lavorare, mentre i materiali più duri possono richiedere strumenti e tecniche specializzate.
- Formazione di trucioli: La formazione e l'evacuazione dei trucioli durante la lavorazione influiscono sull'efficienza del processo e sulla finitura superficiale.
- Usura degli strumenti: Materiali diversi possono causare diversi gradi di usura dell'utensile, incidendo sulla velocità e sui costi di lavorazione.
- Refrigerante e lubrificazione: Un refrigerante e una lubrificazione adeguati sono essenziali per ridurre l'attrito, il calore e l'usura dell'utensile durante la lavorazione.
- Velocità di taglio: La velocità con cui l'utensile da taglio si muove attraverso il materiale influisce sia sulla produttività che sulla qualità della superficie lavorata.
- Materiale dello strumento: La scelta del materiale dell'utensile da taglio, come metallo duro o acciaio super rapido, dipende dal materiale da lavorare.
- Parametri di taglio: La regolazione dei parametri di taglio come la velocità di avanzamento e la profondità di taglio può ottimizzare il processo di lavorazione per materiali specifici.
Macchine Utensili per Lavorazioni di Precisione
Le macchine utensili sono il cuore della lavorazione meccanica di precisione, consentendo la trasformazione delle materie prime in parti di alta precisione. In questa sezione esploreremo quattro tipi chiave di macchine utensili utilizzate nella lavorazione di precisione: centri di lavoro CNC, torni, rettificatrici ed elettroerosione (lavorazione a scarica elettrica). Ciascuna di queste macchine svolge un ruolo unico nella produzione di componenti precisi.A. Centri di lavoro CNC
I centri di lavoro CNC (Computer Numerical Control) sono versatili e ampiamente utilizzati nelle lavorazioni meccaniche di precisione. Sono sistemi automatizzati che controllano il movimento degli utensili da taglio e dei pezzi con eccezionale precisione. Ecco una panoramica dei centri di lavoro CNC e il loro significato:- Versatilità: I centri di lavoro CNC possono eseguire varie operazioni di lavorazione, tra cui fresatura, foratura e maschiatura. Questa versatilità consente la produzione di parti complesse con molteplici caratteristiche.
- Alta precisione: Il controllo computerizzato delle macchine CNC garantisce un posizionamento preciso dell'utensile e risultati costanti, rendendole ideali per pezzi con tolleranze ristrette.
- Automazione: I centri di lavoro CNC possono funzionare ininterrottamente, con un intervento umano minimo. Questa automazione aumenta l’efficienza e riduce il rischio di errori.
- Geometrie complesse: Eccellono nella lavorazione di forme e contorni complessi, rendendoli adatti per settori come quello aerospaziale, dove i componenti complessi sono comuni.
- Risultati ripetibili: Le macchine CNC offrono un'eccellente ripetibilità, garantendo che ogni parte prodotta corrisponda alle esatte specifiche del progetto.
- Tempi di installazione ridotti: I centri di lavoro CNC possono essere programmati per passare rapidamente da un compito all'altro, riducendo al minimo i tempi di configurazione e aumentando l'efficienza della produzione.
B. Torni
I torni vengono utilizzati per creare parti cilindriche ruotando un pezzo mentre un utensile da taglio rimuove il materiale dalla sua superficie esterna. Sono essenziali per produrre alberos, perni e altri componenti con simmetria rotazionale. I punti chiave sulle macchine di tornitura includono:- Parti cilindriche: I torni sono specializzati nella produzione di componenti cilindrici o tubolari, compresi quelli con filettature o scanalature complesse.
- Velocità elevate: Funzionano ad alte velocità, rendendoli adatti a parti che richiedono una finitura liscia e accurata.
- Funzionamento ad asse singolo: La maggior parte dei torni sono ad asse singolo e si concentrano sulla sagomatura della superficie esterna del pezzo.
- Efficiente per la produzione di massa: La tornitura è altamente efficiente per la produzione di pezzi in serie con uno spreco di materiale minimo.
- Tornio: I torni manuali e controllati da CNC sono macchine di tornitura comunemente utilizzate e offrono una vasta gamma di funzionalità.
C. Rettificatrici
Le rettificatrici sono progettate per la finitura superficiale di precisione e la modellatura di materiali duri o abrasivi. Sono fondamentali per ottenere tolleranze estremamente strette e finiture superficiali superiori. Ecco perché le rettificatrici sono importanti:- Precisione a livello di micron: Le rettificatrici possono raggiungere una precisione a livello di micron, rendendole essenziali per le applicazioni che richiedono il massimo livello di precisione.
- Rimozione materiale: Rimuovono materiale per abrasione, consentendo la correzione delle imperfezioni superficiali e ottenendo una levigatezza eccezionale.
- Affilatura di utensili e frese: Oltre alla rettifica superficiale, esistono rettificatrici specializzate per l'affilatura di utensili da taglio e la produzione di profili precisi.
- Varietà di metodi di macinazione: Diversi tipi di rettificatrici, tra cui rettificatrici superficiali, rettificatrici cilindriche e rettificatrici senza centri, soddisfano diverse esigenze di lavorazione.
- Materiali induriti: La rettifica è particolarmente adatta per materiali temprati come acciaio per utensili e ceramica, dove i metodi di lavorazione tradizionali potrebbero essere inefficaci.
D. Elettroerosione (lavorazione per elettroerosione)
L'elettroerosione, o lavorazione a scarica elettrica, è un processo di lavorazione non tradizionale che utilizza scariche elettriche per modellare i materiali. È ideale per creare parti complesse e delicate dove gli strumenti da taglio tradizionali potrebbero causare danni. Gli aspetti chiave dell’EDM includono:- Nessun contatto fisico: L'elettroerosione non comporta il contatto fisico diretto tra l'utensile e il pezzo da lavorare, riducendo al minimo il rischio di usura dell'utensile e danni ai materiali fragili.
- Alta precisione: Può raggiungere un'elevata precisione e qualità di finitura superficiale, anche con materiali eccezionalmente duri.
- Elettroerosione a filo ed elettroerosione a tuffo: Esistono due tipi principali di macchine per elettroerosione: taglio a filo Elettroerosione a filo, che utilizza un elettrodo a filo, ed elettroerosione a tuffo, che utilizza un elettrodo sagomato.
- Forme complesse: L'elettroerosione può produrre forme complesse, come matrici e stampi, con dettagli complessi e caratteristiche fini.
- Zona interessata dal calore: Poiché l'elettroerosione non genera calore sul pezzo, è adatta per materiali sensibili al calore come le leghe aerospaziali.
- Processo lento: L'elettroerosione è relativamente lenta rispetto ad altri metodi di lavorazione, il che la rende particolarmente adatta per lavori di alta precisione e con quantità limitate.
Utensili da taglio e utensili
Gli utensili da taglio sono all'avanguardia nella lavorazione meccanica di precisione, poiché fungono da strumenti che modellano e trasformano le materie prime in parti di alta precisione. In questa sezione esploreremo i vari tipi di utensili da taglio, l'importanza dei rivestimenti degli utensili e i fattori che influenzano la durata e l'usura dell'utensile.A. Tipi di utensili da taglio
La lavorazione di precisione si basa su una vasta gamma di utensili da taglio, ciascuno progettato per compiti e materiali specifici. La scelta dell'utensile da taglio influenza notevolmente l'efficienza e la precisione del processo di lavorazione. Ecco alcuni tipi comuni di utensili da taglio:- end Mills: Le frese sono strumenti versatili utilizzati per le operazioni di fresatura. Hanno più taglienti e possono rimuovere materiale dal pezzo in vari modi, tra cui sfacciatura, contornatura e scanalatura.
- Trapani: Le punte sono progettate per creare fori nei pezzi. Sono disponibili in varie forme, tra cui punte elicoidali, punte centrali e punte indicizzabili.
- Inserti per tornitura: Vengono utilizzati nei torni per modellare parti cilindriche. Gli inserti per tornitura sono disponibili in una varietà di forme e materiali per adattarsi a diverse applicazioni.
- Frese: Le frese sono disponibili in diverse forme, come frese per spianare, mulini a sfere e frese per scanalature, e vengono utilizzate nelle fresatrici per creare varie caratteristiche sul pezzo.
- alesatori: Gli alesatori vengono utilizzati per rifinire e dimensionare fori precedentemente praticati a dimensioni precise. Garantiscono superfici dei fori lisce e precise.
- Rubinetti e matrici: Questi utensili da taglio vengono utilizzati per operazioni di filettatura. I maschi creano filettature interne, mentre le matrici creano filettature esterne.
- Mole: Le mole sono utensili abrasivi utilizzati per la rettifica superficiale di precisione. Sono disponibili in vari materiali abrasivi e granulometrie.
- brocce: Le brocce sono strumenti specializzati utilizzati per tagliare forme e profili interni ed esterni, come sedi per chiavetta e scanalature.
- Svasatori e svasatori: Questi utensili vengono utilizzati per creare rientranze o smussi attorno ai fori fissaggios.
- Barre noiose: Le barre di alesatura vengono utilizzate nelle operazioni di alesatura per allargare con precisione i fori esistenti.
B. Rivestimenti per utensili
I rivestimenti per utensili sono sottili strati di materiale applicati agli utensili da taglio per migliorarne le prestazioni e la durata. Questi rivestimenti offrono diversi vantaggi:- Attrito ridotto: Rivestimenti come il nitruro di titanio (TiN) e il carbonitruro di titanio (TiCN) riducono l'attrito tra l'utensile e il pezzo da lavorare, garantendo un taglio più fluido e una maggiore durata dell'utensile.
- Durezza migliorata: I rivestimenti aumentano la durezza della superficie dell'utensile, rendendolo più resistente all'usura e prolungando la durata dell'utensile.
- Resistenza al calore migliorata: I rivestimenti possono resistere alle alte temperature generate durante la lavorazione, riducendo l'usura dell'utensile dovuta al calore e aumentando le velocità di taglio.
- Proprietà anti-accumulo: Alcuni rivestimenti hanno proprietà antiadesive, prevenendo l'accumulo di materiale sui taglienti dell'utensile.
- Lubrificazione aumentata: Gli utensili rivestiti hanno un potere lubrificante migliorato, riducendo la necessità di un eccessivo refrigerante e migliorando l'evacuazione del truciolo.
C. Durata e usura dell'utensile
Comprendere la durata e l'usura dell'utensile è fondamentale per ottimizzare i processi di lavorazione e ridurre al minimo i costi di produzione. La durata dell'utensile si riferisce alla durata in cui un utensile da taglio rimane efficace prima di richiedere la sostituzione o il ricondizionamento. Diversi fattori influenzano la durata e l’usura dell’utensile:- Velocità di taglio: Velocità di taglio più elevate possono comportare una maggiore usura dell'utensile a causa delle temperature più elevate generate durante la lavorazione. La corretta selezione delle velocità di taglio è essenziale per bilanciare durata dell'utensile e produttività.
- Tasso di alimentazione: La velocità con cui l'utensile da taglio avanza nel pezzo in lavorazione influisce sull'usura dell'utensile. Velocità di avanzamento elevate possono accelerare l'usura, mentre velocità di avanzamento inferiori possono prolungare la durata dell'utensile.
- Profondità di taglio: La profondità di taglio influenza la quantità di materiale rimosso per passata. I tagli più profondi possono aumentare l’usura dell’utensile, quindi l’ottimizzazione della profondità è fondamentale.
- Durezza del materiale: Il taglio di materiali duri può accelerare l'usura dell'utensile. Strumenti e rivestimenti specializzati vengono utilizzati per lavorare efficacemente materiali duri.
- Refrigerante e lubrificazione: Un refrigerante e una lubrificazione adeguati aiutano a dissipare il calore e a ridurre l'attrito, prolungando la durata dell'utensile.
- Materiale dello strumento: Il materiale di cui è fatto l'utensile da taglio influisce sulla sua resistenza all'usura. Materiali come il carburo e la ceramica offrono un'eccellente resistenza all'usura.
- Geometria dell'utensile: La geometria dell'utensile da taglio, compreso l'angolo di spoglia, l'angolo di scarico e il design del rompitruciolo, svolgono un ruolo significativo nei modelli di usura.
- Materiale del pezzo: Il tipo di materiale in lavorazione influisce sull'usura dell'utensile. I materiali abrasivi possono portare ad un'usura più rapida dell'utensile.
Processi di lavorazione di precisione
I processi di lavorazione di precisione sono i metodi attraverso i quali le materie prime vengono trasformate in parti di alta precisione con tolleranze strette e finiture superficiali eccezionali. In questa sezione esploreremo cinque processi chiave di lavorazione meccanica di precisione: tornitura, fresatura, foratura, rettifica ed elettroerosione (EDM). Ciascuno di questi processi ha uno scopo unico e viene utilizzato in base ai requisiti specifici del pezzo.R. Girando
La tornitura è un processo di lavorazione utilizzato principalmente per modellare parti cilindriche. Implica la rotazione di un pezzo mentre un utensile da taglio a punto singolo rimuove il materiale dalla superficie esterna. Ecco gli aspetti chiave della tornitura:- Parti cilindriche: La tornitura è ideale per la produzione di componenti cilindrici come alberi, perni e manicotti.
- Simmetria rotazionale: È particolarmente adatto per le parti che richiedono simmetria rotazionale, poiché il pezzo ruota su un tornio mentre l'utensile da taglio lo modella.
- Varie operazioni: La tornitura può eseguire varie operazioni, tra cui sfacciatura, tornitura (riduzione del diametro), tornitura conica e filettatura.
- Taglio a punto singolo: Un singolo utensile da taglio rimuove il materiale con un movimento continuo, con conseguente rimozione efficiente del materiale.
- Tornio: Per le operazioni di tornitura vengono comunemente utilizzati sia i torni manuali che quelli controllati da CNC.
B. Fresatura
La fresatura è un processo di lavorazione di precisione versatile che impiega utensili da taglio multipunto per rimuovere materiale da un pezzo. È adatto per creare un'ampia gamma di forme e caratteristiche. Gli aspetti chiave della fresatura includono:- Versatilità: La fresatura può produrre superfici piane, fessure, tasche e contorni complessi. Viene utilizzato sia per la lavorazione 2D che 3D.
- Taglio multipunto: Più taglienti sull'utensile interagiscono simultaneamente con il pezzo in lavorazione, consentendo un'efficiente rimozione del materiale.
- Tipi di fresatura: La fresatura può essere eseguita utilizzando vari tipi di frese, tra cui frese a candela, frese a spianare e mulini a sfere.
- Centri di lavoro CNC: Le fresatrici a controllo CNC offrono un controllo preciso sul movimento dell'utensile e sono ampiamente utilizzate nella lavorazione moderna.
- Velocità elevate: La fresatura può essere eseguita a velocità elevate, consentendo una produzione efficiente.
C. Perforazione
La foratura è un processo di lavorazione di precisione utilizzato per creare fori nei pezzi. È un’operazione fondamentale in diversi settori. Gli aspetti chiave della perforazione includono:- Creazione del foro: Le perforatrici utilizzano strumenti specializzati chiamati trapani per rimuovere materiale e creare fori di diametri specifici.
- Tipi di esercitazioni: Sono disponibili diversi tipi di punte, comprese punte elicoidali, punte centrali e punte indicizzabili, ciascuna progettata per applicazioni specifiche.
- Precisione: Il posizionamento e l'allineamento precisi sono essenziali nella perforazione per garantire che i fori vengano creati con precisione.
- Velocità e velocità di avanzamento: I parametri di foratura come la velocità di rotazione e la velocità di avanzamento sono fondamentali per ottenere le dimensioni del foro desiderate.
- Refrigerante e lubrificazione: Vengono utilizzati refrigerante e lubrificazione adeguati per dissipare il calore e ridurre l'attrito durante la perforazione.
D. Rettifica
La rettifica è un processo di lavorazione di precisione che utilizza mole abrasive per rimuovere materiale e ottenere tolleranze e finiture superficiali estremamente strette. Gli aspetti chiave della macinazione includono:- Precisione eccezionale: La rettifica può raggiungere una precisione a livello di micron, rendendola ideale per applicazioni che richiedono la massima precisione.
- Finitura di superficie: Produce finiture superficiali superiori, spesso eliminando la necessità di ulteriori processi di finitura.
- Materiali: La rettifica è adatta per materiali duri e abrasivi, tra cui acciaio temprato, ceramica e carburi.
- Varietà di metodi di macinazione: Diversi tipi di rettificatrici, come rettificatrici superficiali, rettificatrici cilindriche e rettificatrici senza centri, soddisfano le diverse esigenze di lavorazione.
- liquido di raffreddamento: Un liquido refrigerante adeguato è essenziale nella rettifica per prevenire il surriscaldamento e mantenere l'integrità della mola.
E. Macchina per elettroerosione (EDM)
L'elettroerosione, o lavorazione a scarica elettrica, è un processo di lavorazione di precisione non tradizionale che utilizza scariche elettriche per rimuovere materiale. È particolarmente adatto per la lavorazione di forme complesse e complesse, nonché di materiali duri e resistenti al calore. Gli aspetti chiave dell’EDM includono:- Lavorazione senza contatto: L'EDM non comporta il contatto diretto tra l'utensile e il pezzo da lavorare, riducendo il rischio di usura e danneggiamento dell'utensile.
- Alta precisione: L'elettroerosione può raggiungere un'elevata precisione, rendendola adatta per applicazioni in cui sono essenziali tolleranze strette.
- Forme complesse: Eccelle nella lavorazione di forme complesse, matrici, stampi e componenti con dettagli fini.
- Elettroerosione a filo ed elettroerosione a tuffo: Esistono due tipi principali di macchine per elettroerosione: l'elettroerosione a filo, che utilizza un elettrodo a filo, e l'elettroerosione a tuffo, che utilizza un elettrodo sagomato.
- Processo lento: L'elettroerosione è relativamente lenta rispetto ad altri metodi di lavorazione, il che la rende particolarmente adatta per lavori di alta precisione e con quantità limitate.
Tolleranze e controllo qualità
La lavorazione di precisione richiede un'attenzione meticolosa ai dettagli e un impegno rigoroso nel controllo di qualità per garantire che le parti soddisfino gli standard specificati. In questa sezione esploreremo tre aspetti critici del controllo di qualità nella lavorazione di precisione: dimensionamento e tolleranza geometrica (GD&T), controllo statistico del processo (SPC) e garanzia di qualità.A. Dimensionamento e tolleranza geometrica (GD&T)
La quotatura e tolleranza geometrica, spesso abbreviata in GD&T, è un sistema utilizzato per definire e comunicare le variazioni consentite in termini di dimensioni, forma, orientamento e posizione delle caratteristiche su una parte. GD&T è vitale nella lavorazione meccanica di precisione per i seguenti motivi:- Comunicazione precisa: GD&T fornisce un linguaggio standardizzato a ingegneri, progettisti e macchinisti per comunicare in modo accurato l'intento progettuale e i requisiti dimensionali.
- Chiarimento sulla tolleranza: Aiuta a definire la variazione accettabile nelle dimensioni critiche, garantendo che tutte le parti interessate comprendano le deviazioni consentite.
- Qualità migliorata: GD&T promuove il miglioramento della qualità riducendo l'ambiguità nelle specifiche di progettazione, minimizzando il rischio di errori durante la lavorazione.
- Razionalizzazione dei costi: Specifiche GD&T chiare possono portare a costi di produzione ridotti, poiché è meno probabile che le parti vengano scartate o richiedano rilavorazioni a causa di incomprensioni o interpretazioni errate.
- Geometria complessa: È particolarmente utile per parti con geometrie complesse, garantendo che tutte le caratteristiche siano prodotte secondo le specifiche desiderate.
B. Controllo statistico del processo (SPC)
Il controllo statistico del processo (SPC) è una metodologia di controllo della qualità che utilizza tecniche statistiche per monitorare e controllare il processo di lavorazione. L'SPC è essenziale nelle lavorazioni meccaniche di precisione per i seguenti motivi:- Monitoraggio del processo: SPC aiuta a monitorare i processi di lavorazione in tempo reale, identificando variazioni o deviazioni rispetto ai parametri desiderati.
- Rilevamento precoce dei problemi: Monitorando continuamente il processo, SPC consente il rilevamento tempestivo di problemi che potrebbero portare a parti fuori specifica, riducendo sprechi e rilavorazioni.
- Processo decisionale basato sui dati: SPC si basa su dati e analisi statistiche per prendere decisioni informate sugli adeguamenti del processo, garantendo che il processo di lavorazione rimanga entro limiti accettabili.
- Coerenza migliorata: L'SPC promuove la coerenza del processo e riduce la probabilità di produrre parti non conformi.
- Scarti e rilavorazioni ridotti: Identificando e affrontando tempestivamente le variazioni del processo, SPC riduce al minimo la produzione di parti difettose, riducendo i costi di scarto e rilavorazione.
C. Garanzia di qualità nella lavorazione meccanica di precisione
La garanzia della qualità nella lavorazione meccanica di precisione comprende un approccio globale per garantire che le parti prodotte soddisfino o superino gli standard di qualità specificati. Coinvolge vari elementi, tra cui:- Documentazione del processo: La documentazione dettagliata dei processi di lavorazione, comprese le procedure operative standard (SOP) e le istruzioni di lavoro, garantisce che ogni fase venga eseguita in modo coerente.
- Ispezione e misurazione: Ispezioni e misurazioni rigorose utilizzando strumenti di precisione e tecniche metrologiche verificano che le parti siano conformi alle tolleranze e agli standard di qualità specificati.
- Calibrazione: La calibrazione regolare delle attrezzature di lavorazione e degli strumenti di misura è essenziale per mantenere l'accuratezza e la tracciabilità.
- Verifica materiale: La verifica delle proprietà, della composizione e della qualità del materiale è fondamentale per garantire che il materiale utilizzato soddisfi i requisiti di progettazione.
- La formazione dei dipendenti: I programmi di formazione e sviluppo delle competenze per macchinisti e personale addetto al controllo qualità garantiscono che siano competenti nei loro ruoli e responsabilità.
- Analisi della causa principale: Quando vengono identificate parti non conformi, viene condotta un'analisi della causa principale per determinare l'origine del problema e implementare azioni correttive.
- Miglioramento continuo: Una cultura di miglioramento continuo promuove l'innovazione e guida i miglioramenti continui nei processi di lavorazione e nelle procedure di controllo della qualità.
- Feedback del cliente: La raccolta e l'analisi del feedback dei clienti aiuta a identificare le aree di miglioramento e ad allineare i processi di lavorazione alle aspettative dei clienti.
Conclusione
A. L'arte e la scienza della lavorazione meccanica di precisione
La lavorazione di precisione si trova all’intersezione tra arte e scienza, dove creatività, abilità e innovazione convergono per produrre parti di alta precisione che guidano le industrie e modellano il mondo moderno. È sia una forma d'arte, che richiede la maestria e l'esperienza dei macchinisti che trasformano le materie prime in opere di eccellenza ingegneristica, sia una scienza che si basa su tecnologia all'avanguardia, scienza dei materiali e processi avanzati per ottenere una precisione senza precedenti. Il viaggio della lavorazione meccanica di precisione ci porta attraverso la comprensione dei materiali e delle loro proprietà, la padronanza degli strumenti e dei macchinari da taglio e il controllo meticoloso dei processi e delle tolleranze. Comprende il linguaggio del dimensionamento e delle tolleranze geometriche, la vigilanza del controllo statistico dei processi e l'impegno per la garanzia della qualità. La lavorazione di precisione svolge un ruolo fondamentale in diversi settori, da quello aerospaziale e automobilistico ai dispositivi medici e all'elettronica, dando forma a qualsiasi cosa, dai motori aeronautici alle articolazioni artificiali e ai microchip. Consente la creazione di componenti che funzionano con precisione e affidabilità senza pari, spesso spingendo i limiti di ciò che è possibile.B. Considerazioni finali
Concludendo questa esplorazione della lavorazione meccanica di precisione, è chiaro che questo campo non riguarda solo la creazione di parti; si tratta della creazione di possibilità. La ricerca della precisione guida l’innovazione, spingendo oltre i limiti di ciò che può essere raggiunto. Che si tratti della delicata lavorazione artigianale necessaria per creare gli intricati ingranaggi di un orologio o della tecnologia avanzata necessaria per produrre complessi componenti aerospaziali, la lavorazione meccanica di precisione è al centro di tutto. Il futuro della lavorazione meccanica di precisione è pieno di promesse. I progressi nella scienza dei materiali, nell’automazione e nelle tecnologie digitali continuano a rimodellare il panorama. La miniaturizzazione, la stampa 3D e le pratiche di produzione sostenibili stanno diventando sempre più importanti, inaugurando nuovi orizzonti per il settore. In un mondo in cui la precisione conta più che mai, la lavorazione meccanica di precisione rimane un pilastro indispensabile dell’ingegneria moderna. È una testimonianza dell’ingegno umano e della nostra costante ricerca dell’eccellenza in ogni aspetto della produzione. Man mano che cresce la richiesta di maggiore precisione e di componenti più complessi, la lavorazione meccanica di precisione continuerà ad evolversi, affrontando le sfide di domani con la stessa dedizione e precisione che l’hanno definita per secoli.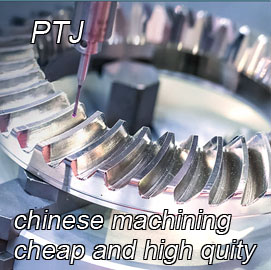
I nostri servizi
- Lavorazione a 5 assi
- Fresatura a controllo numerico
- Tornitura cnc
- Industrie di lavorazione
- Processo di lavorazione
- Trattamento della superficie
- Lavorazione dei metalli
- Lavorazione plastica
- Stampo per metallurgia delle polveri
- Die Casting
- Galleria delle parti
Casi Studio
- Parti metalliche per auto
- Pezzi meccanici
- Dissipatore di calore a LED
- Parti di costruzione
- Parti mobili
- Parti mediche
- Parti elettroniche
- Lavorazione su misura
- Parti di biciclette
Lista materiali
- Lavorazione dell'alluminio
- Lavorazione del titanio
- Lavorazione dell'acciaio inossidabile
- Lavorazione del rame
- Lavorazione dell'ottone
- Lavorazione Super Lega
- Peek lavorazione
- Lavorazione UHMW
- Lavorazione Unilate
- Lavorazione PA6
- Lavorazione PPS
- Lavorazione Teflon
- Lavorazione Inconel
- Lavorazione dell'acciaio per utensili
- Più materiale
Galleria delle parti